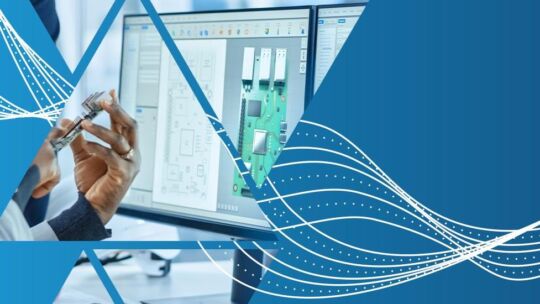
Why start from scratch? You can customize any of our high-quality reference designs to get a jumpstart on developing your product design.
You’ll cut major costs and scale your manufacturing faster.
An idea can feel light years from a launch. But a high-quality prototype can shorten the distance.
Prototyping brings your idea into its first functional, tangible form. Make it faster and more cost-effective with 3D printing and additive manufacturing. We help you stay on track to meet your milestones and deadlines. And we’ll do it where it makes sense for you. You can prototype out of a site local to your operations, before ramping up to full volume in a region that meets your needs.
Bring your product to market safely thanks to our full suite of testing: electrical, mechanical, thermal, and chemical.
We test at both the component and completed product levels. You can have confidence that you’re within regulatory standards, avoiding costly setbacks and delays.
Through all possible scenarios and conditions, you need to know your product works as intended. We perform reliability testing at both the component and final product levels to reduce setbacks and delays.
We test your product in environmental chambers that simulate temperature, humidity, salt spray, ultraviolet rays, lighting, and drop and abrasion testing. We use contemporary techniques such as CT scan, X-Ray, Shadow Moiré, and SEM.
We miniaturize the microelectronics within your product and prepare it to scale. Our technical capabilities include high-density SMT and fine-pitch flip chip, precision die attach and wire bonding, and robust encapsulation techniques with an emphasis on thermal management, miniaturization, size reduction, and performance enhancement.
Our experience with system in package (SiP) gives you miniaturized design, better functionality, and faster time to market.
Our simulation and modeling checks for product viability and potential pitfalls, saving you the time and money of testing it in the real world. So you’ll know about any high-risk components or parts before the product even exists. No crystal ball necessary.
You have your product design — now let’s make sure you can scale it. We help you identify opportunities and unexpected challenges in the manufacturing process. Our design for manufacturing (DfM) guidance can make your product work better, become more customizable, have fewer parts, and cut down non-recurring costs.
Our approach to DfM helps you maximize your investments, reduce your time-to-market, and eliminate the risk of discovering design issues in full-scale production.
Let us position your product design to deliver the highest yield at the fastest time-to-market well before it reaches the manufacturing stage.
Using our DfM solutions, we can help you make key design adjustments that eliminate scrap and bottlenecks while maximizing product performance.
We make sure your design is poised to incorporate the most cost-effective and efficient processes while deploying materials management, quality control, and more.
In fact, we take our analysis down to the individual parts level with Design for Manufacturing and Assembly (DFMA). That way, you can reduce the number of individual parts and assembly steps for more consistent build quality.
Find out before you scale through Finite Element Analysis (FEA).
Protect your future hardware from defects using DfT.
New technologies, materials, and advanced circuitries make the task more challenging — but Design for Reliability (DfR) can help prolong a high level of performance throughout the lifecycle.
You can’t go faster than automation, but you can make sure automated manufacturing goes its fastest with DDFAUT.
We can help you speed things along even more using our expertise in PCBA Panel Array, so parts load at a much faster rate. And don’t let ever-increasing parts shortages delay development when you design for maximum interchangeability with Design for Tolerance Stack-up Analysis (DFTSA).