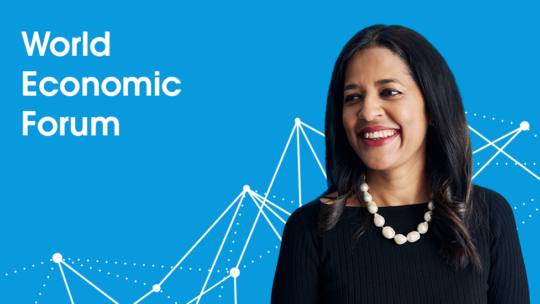
If a crisis brings out people’s true character, what does the COVID-19 pandemic tell us about the Flex family? For those who worked tirelessly to ensure our frontline production teams were equipped with proper personal protection equipment (PPE), being united by a common goal went beyond collegial collaboration.
Everyone felt privileged to help so we all jumped in.
— Ivan Prnja, Global Team Lead for Mask Production
(Conception to Distribution)
Getting ahead of PPE supply risks
In March 2020, Flex leaders discussed making our own face masks to help protect our employees working at our production facilities. Amid PPE export restrictions and border closures, we wanted to get ahead of potential PPE supply shortages and minimize our impact on vital PPE supplies required by essential healthcare workers.
We designated ten sites around world to produce masks, and once in mass production, each site would regionalize its supply sources to mitigate logistical risks. After all, at the height of the pandemic, border closures were unpredictable while air capacities were greatly reduced.
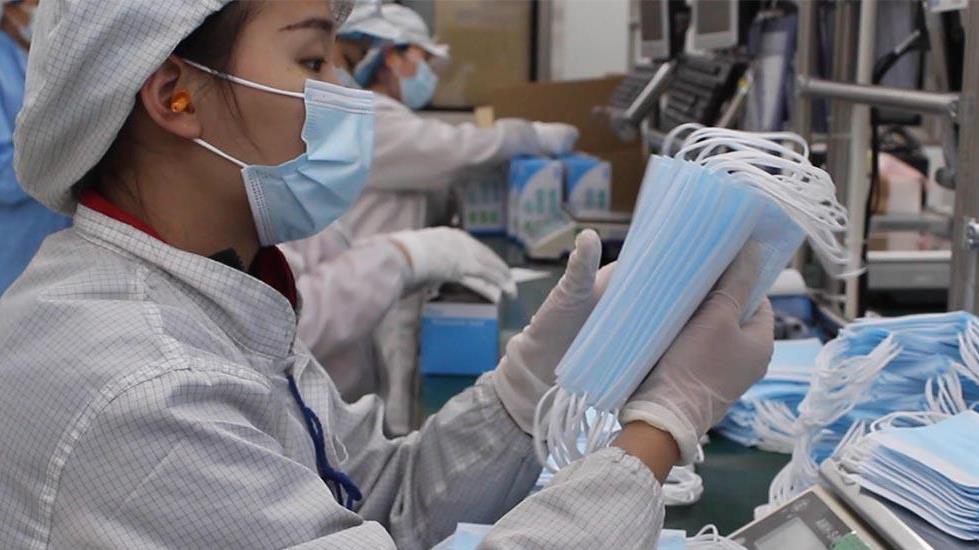
Flex had never made a single mask in our 51-year history. Planning through production usually requires months for most products, where specialists in design, engineering, quality, operations, and materials typically collaborate and devise a path forward.
So how is it that four weeks following our decision to produce our own masks, about a million units rolled off the production line in Zhuhai, China?
Moving fast with purpose and discipline
When the whole world was in overdrive to put a mask on every face, sourcing production equipment and materials was a major challenge. “The market was brutal,” says Hugo Montes of the indirect procurement team. He and his colleagues looked everywhere for material, identifying some 2,000 material suppliers in just two weeks.
Meanwhile, we skipped all the normal processes to develop assembly lines. Normally, we would nurture a local support team to engineer, train, install, troubleshoot, and test the equipment, then develop spares. Instead, we built, troubleshooted, and readied the equipment with our vendor within just weeks.
Once we had the machines in working order, we had four to six weeks to ship them to our production sites where more fine tuning would be required. When we were ready to ship to Tczew, Poland, the last site on our list, we chose rail because ocean freight was severely constrained, and we couldn’t get confirmation that it would arrive in two to three weeks. With rail, we could get an ETA so it was less risky.
Supporting each other while finding a better way
Initially, we didn’t know how to use the mask production equipment and the materials were generally unlike any inputs we’ve worked with. As our production machinery and “starter kit” materials were sourced from China, Flex Zhuhai was the first to ramp. The team immediately shared their learnings with others. As more sites ramped up, more colleagues gave tips to those who were readying to begin production. Despite the language barriers, we managed to communicate and made it work.
We collaborated in the truest sense of the word. Whenever one site experienced hiccups, others rushed to help. When a team ran short on material, another site covered by sharing its materials. If an equipment did not work well with the fabric, a team member often tapped other teams for help so they didn’t have to reject the material. As the teams constantly shared best practices, we began mastering mask production. We continue to trade tips to enhance quality, accelerate output, and reduce costs.
Completing the race to plan, procure supplies, manufacture, test, and provide around-the-clock troubleshooting by dedicated team members in just weeks was “nothing short of a miracle,” according to Ivan.
We are experts in many things — from electronics to plastics to metals — but not masks! The fact that we did this in such a record time was unbelievable.
— Ivan Prnja
Doing the right thing, always
While our masks are not for surgical use, we were conscientious about sourcing high-quality materials that not only meet protective standards but also demonstrated low potential to cause allergies and irritations. We put our finished masks to rigorous testing — the kind of third-party testing required for securing certifications. We sent every combination of the materials we considered using to third-party testing labs and chose the highest-scoring combinations of materials.
I wanted to make sure we can stand behind the masks we are producing. This is something our teammates, our friends in the Flex family and their families will wear on their faces.
— Alejandro Armendariz, Indirect Procurement Team
After four months, we got really good at mask-making.
How good? We donated masks to our employees’ families and local communities and provided them to customers at cost.
I’ve been at Flex for more than 10 years, and I’ve never been more proud of our team.
— Paul Baldassari, EVP and Program Sponsor
For a deeper dive, please see: Producing face masks to protect our employees, page 47, in our book, “Resilience in a crisis: a manufacturer’s perspective.”