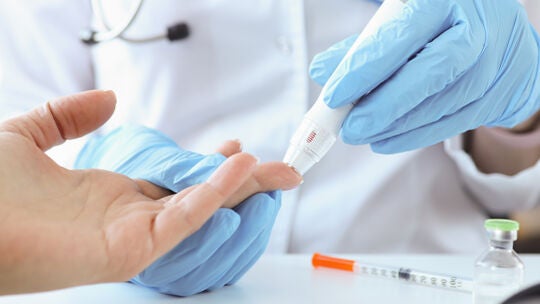
Executive summary
In almost every sector that produces a physical product, there is pressure to bend the traditional linear production model to become more circular, creating environmentally friendly and sustainable products that ultimately do not compromise safety. The healthcare industry is no exception, though manufacturers must balance more sustainable design and manufacturing with the strict regulations and requirements that are in place to safeguard patient health.
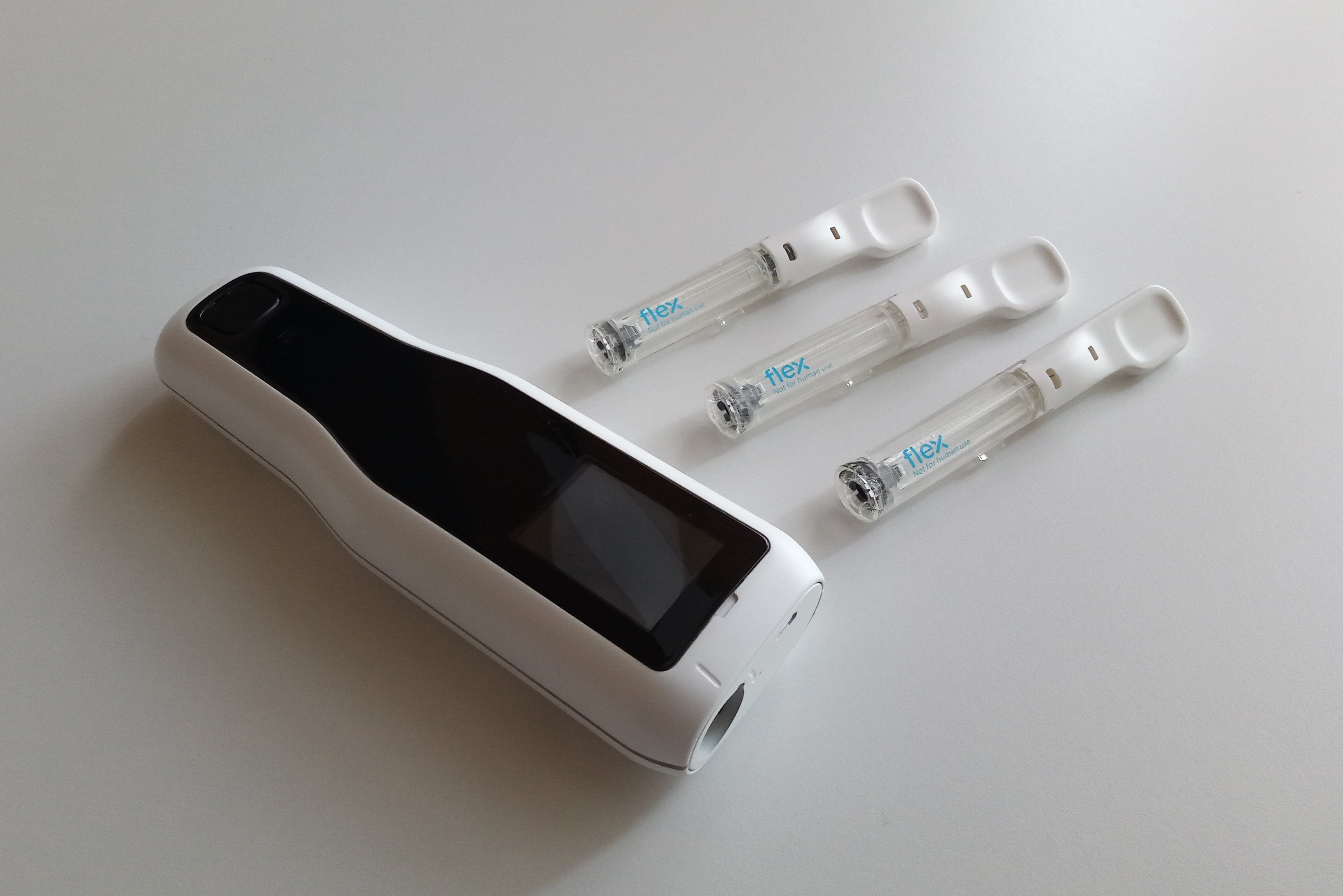
In this white paper, we will discuss how product engineers can perform an Eco-Value Analysis to demonstrate the benefits of an eco-smart design that accounts for sustainable materials, product durability, and improved energy efficiency. We will also cover how using lifecycle assessments based on quantitative data and making other improvements to the platform allows for a product that meets the growing demand for environmental goals.
Finally, we will demonstrate how applying Design for Environment (DfE) guidelines empowers our healthcare solutions customers to achieve immediate reductions to in-market and future products that lower the environmental impacts of manufacturing processes.
Introduction
The World Health Organization estimates that about 85% of overall waste in healthcare is a general, non-hazardous waste. The call to action for more sustainable healthcare means designing solutions that adopt recyclable options, enable circular economy processes, and increase product durability. The ultimate goal is to minimize waste and contribute to a greener planet without compromising device reliability or patient safety.
As the focus on waste reduction, getting more value from resources, and lowering the environmental footprint of manufacturing is shifting industries, medical device manufacturers must integrate sustainability into their requirements. Alongside the larger manufacturing industry, medical device manufacturers must move away from historic “take, make, and dispose of” linear models and towards a regenerative, closed-loop product lifecycle through repair, refurbishment, and reuse efforts.
Doing so requires a close look at how products are currently designed and made, lifecycle assessments, and a willingness to implement product redesigns that reduce overall waste and advance sustainability goals.
Identifying improvements with an Eco-Value Analysis
The first step is performing an Eco-Value Analysis to begin the redesign assessment. This assessment is carried out against a set of best-practice guidelines to identify where improvements can be made.
Example areas that can be identified for improvements:
- Use of sustainable materials
- Extending product durability
- Improving energy efficiency
- Ease disassembly and reassembly processes
- Ease maintenance and repair processes
Instead of only looking at one element of the design, medical device manufacturers must evaluate each product characteristic for potential redesign, which will provide a fuller picture for how to meet increasingly ambitious sustainability targets. Each outlined focus area can be assessed regarding design impact and potential environmental benefits. The different possible design changes identified by the Eco-Value Analysis can be categorized by time, complexity phasing, and scope of effort to determine the best path forward.
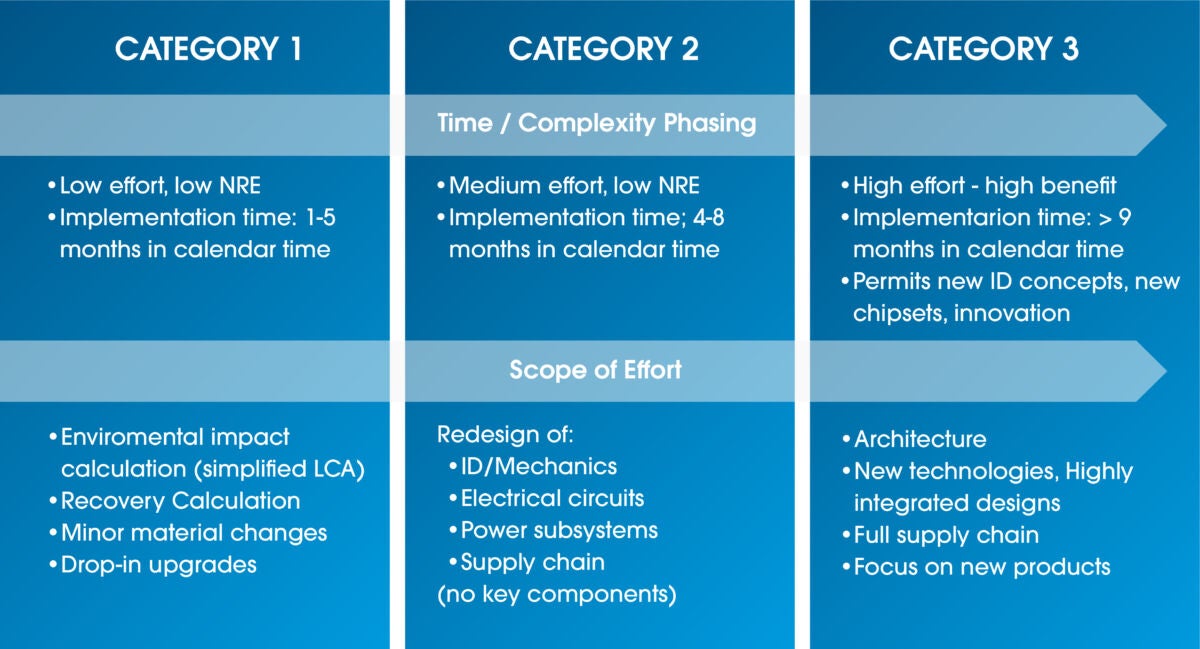
Figure 1: Eco-Value Analysis
Specifically for medical devices, design principles are traditionally geared to meet performance and reliability requirements. The need for more focus on sustainability is evident in materials selected for some earlier generation products.
For example, product exteriors can be painted for aesthetic reasons or to incorporate a soft-touch grip. From a sustainability perspective, these additions can act as contaminators with a negative impact on the product’s recyclability.
As a safety precaution and to prevent access to the PCBA, the plastic exterior is often sealed with a weld or other irreversible assembly solution. As a result of this anti-tampering feature, the product cannot be easily disassembled for physical maintenance, repair, or refurbishing of parts without the risk of permanent damage to the external case and potentially the internal components, too.
Another example relates to firmware upgrade considerations. Some products do not allow firmware to be upgraded on products already deployed in the field. While this security restriction prevents interference from a malicious user, the device must be replaced when new features or bug fixes are available, as it can’t be upgraded physically. In this case, Eco-Value Analysis may influence the product developer to enable remote firmware maintenance capabilities.
Application of eco-smart by design
Medical devices should utilize Design for Environment (DfE) guidelines to help reduce their environmental impact through considerations like material selection and material reduction. By understanding the benefits of an Eco-Value Analysis, designers can further evaluate designs to determine how best to build or redesign products that allow for ease of disassembly, reassembly, maintenance, and repair. These design processes can improve the reliability and durability of products, extending their life and helping to mitigate single-use products that contribute to waste.
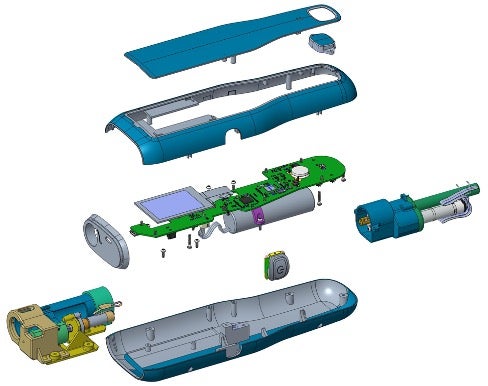
One example of this design process utilization is the smart autoinjector design platform (Figure 2). The autoinjector is a medical device built around DfE guidelines to reduce its environmental footprint and address areas of improvement for product sustainability identified in many drug delivery devices on the market today.
The platform was designed to enable MedTech and pharmaceutical companies to accelerate time-to-market, reduce costs, and boost reliability while ensuring patient compliance and sustainability needs.
Figure 2: Smart Autoinjector Platform
In the healthcare industry, we must consider new sustainability demands alongside the functional requirements that have been developed and honed through years of experience. Looking to the future, we must integrate Design for Environment principles
into the product design process so that we can continue to save lives while also safeguarding the planet.
— Stefano Vicenzetto, Senior Design Systems Engineer
The Smart Autoinjector platform uses numerous eco-smart designs, such as:
- Long-life rechargeable batteries instead of disposable non-rechargeable ones
- Secure remote upgrades for firmware on the autoinjector platform
- Developing smaller subsystems and PCBA systems that use fewer materials lowers the overall CO2 emissions
- Easy disassembly, better-enabling repair, refurbishment, or parts separation for reusing, recycling, or disposal
The assembly process for the autoinjector platform has been designed with a uniform screw design instead of techniques like laser welding, ultrasonic welding, or heat staking. The utilization of uniform screws ensures the autoinjector can be unscrewed using a single tool, speeding up and simplifying the disassembly when needed.
The Flex design adheres to DfE guidelines and principles by minimizing welding and gluing of internal products during the assembly and manufacturing process, which results in benefits even at the end-of-life stage. Because of the lower contamination of materials being recycled, the design continues contributing to lower waste targets.
Lifecycle assessments for environmental impact
Along with the eco-smart design considerations when developing the autoinjector platform, a cradle-to-gate lifecycle assessment was performed to evaluate environmental impacts based on the following:
- CO2 emissions
- Energy and water consumption
- Recycling rate (percentage of material recycled)
- Recovery rate (percentage of material used to generate energy when the product reaches the end of life)
The assessment results (Figure 3) allowed for identifying the potential environmental impacts of the various components used for manufacturing. With the implementation of the DfE guidelines, the partnerships with MedTech companies allow for the creation and execution of eco-friendly strategies to achieve their sustainability objectives.
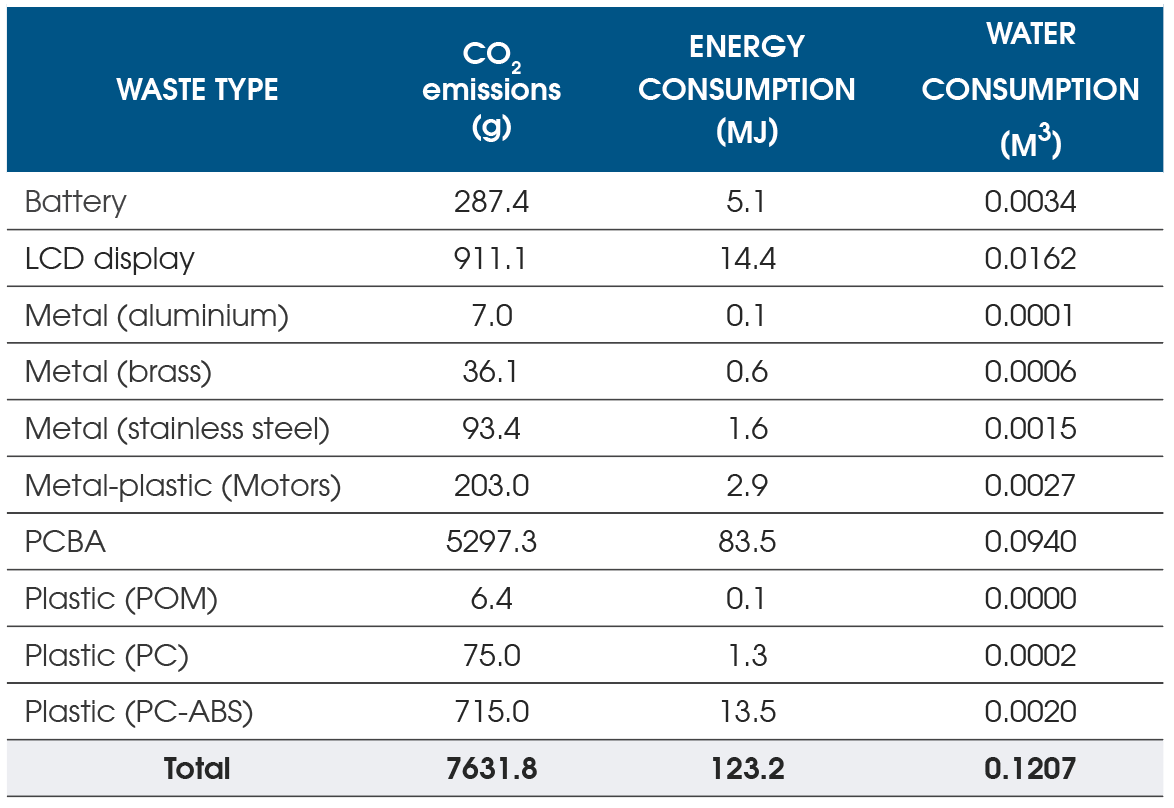
Figure 3: Lifecycle Assessment
Specifically evaluating the CO2 equivalent emissions (Figure 4), it is possible to calculate the benefit of implementing a particular design to increase durability or enable easy disassembly.
By doubling the reliability requirements of the PCBA subsystem over the expected autoinjector usage cycles, the PCBA could be reused for refurbished devices, saving up to 69% on the CO2 emission, and by including the LCD in the refurbishment strategy, the CO2 saving could rise to 81%.
Another method to decrease CO2 emissions is to reduce the mass of all the plastic parts, particularly for external covers and the lens. Finite element analysis can be used to optimize the overall thickness, which ad hoc tests like free-fall or impact tests can support.
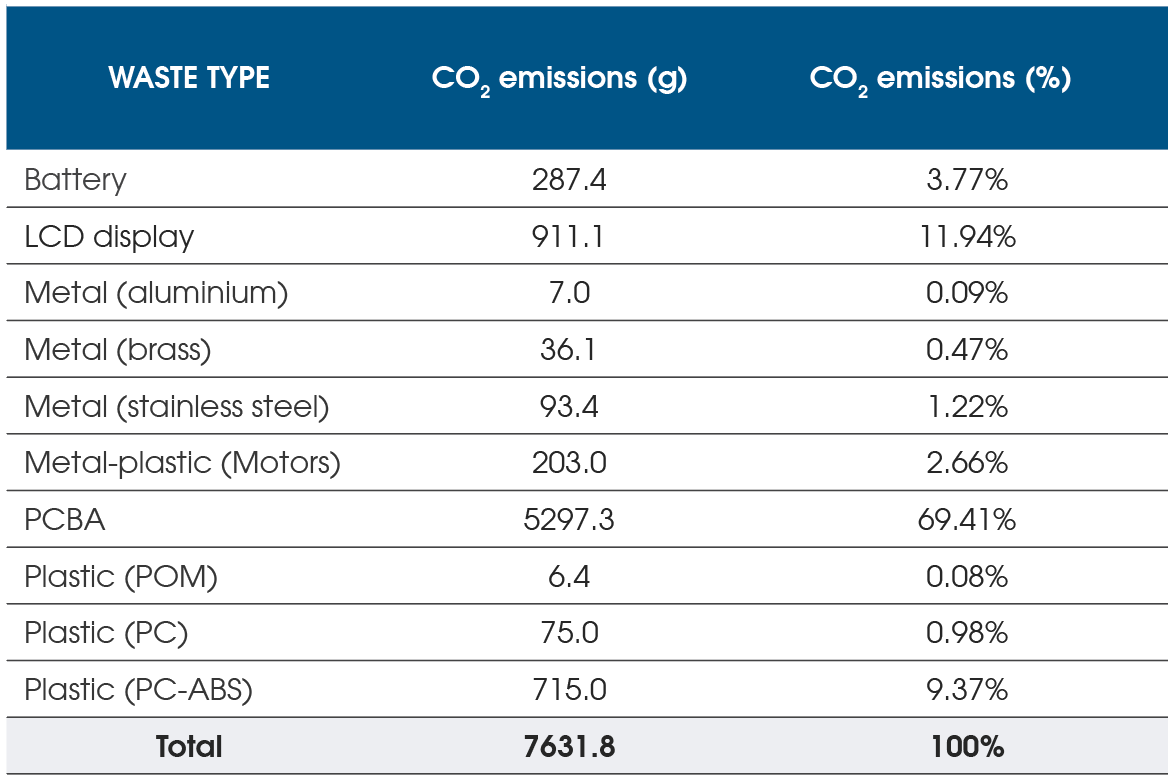
Figure 4: Lifecycle Assessment — CO2 Equivalent Emission
Sustainability goals can be enhanced even further by selecting recyclable materials (Figure 5). The Design for Disassembly approach allows materials to be collected and separated at the end of the product’s life. Certain materials could be diverted from landfill and used for other purposes like recycled as raw materials to manufacture non-medical products or energy recovery.
Overall, the recovery and recycling rate assessed for the smart autoinjector platform could achieve a 76.2% recycling rate (recycled material / total material weight) and a 91.2% recovery rate (recycled and recovered material / total material weight).
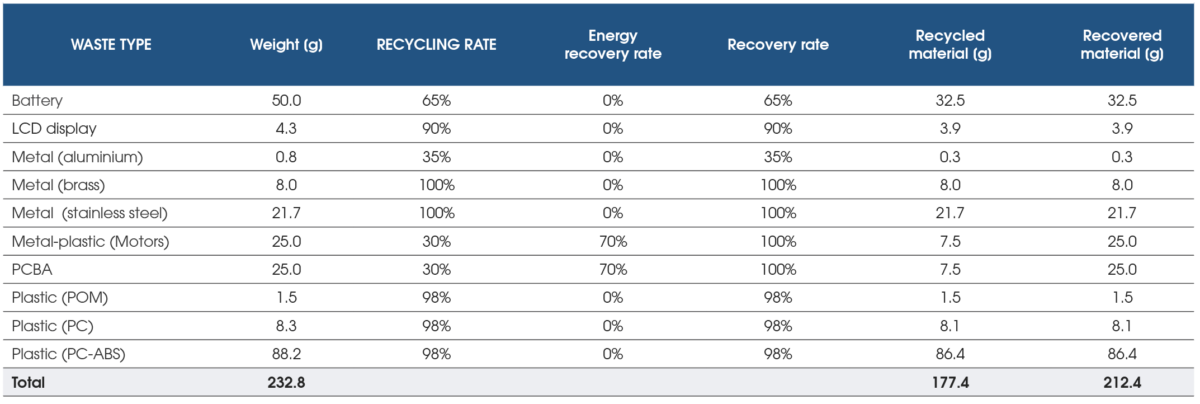
Figure 5: Recovery and Recycling Rate
Continuous improvements to product design
As mentioned, recyclable plastics were selected for the autoinjector platform in the early design phase. A further step is replacing the standard fossil-based plastics with new greener plastics generated by virgin biomass (vegetation) and cooking oils with a lower environmental footprint.
One example is a new polycarbonate that the manufacturer defined as climate-neutral that could be used to replace all the external covers, considerably reducing the associated emissions. The same replacement can also be done for the lens, initially produced in fossil-based bisphenol-A polycarbonate. A similar approach can also be used for the parts in polyoxymethylene (POM).
Another optimization process is focused on power consumption
By optimizing power consumption, we can replace the battery with a smaller, rechargeable one. This results in several benefits:
- A reduction in the CO2 equivalent emissions in the cradle-to-gate lifecycle assessment
- A reduction in the energy needed to recharge the autoinjector platform’s battery during use
- A reduction of hazardous waste during the disposal of the products
Ultimately, medical device manufacturers can adopt principles of continuous improvement to evaluate a product’s design on an ongoing basis and implement new ways to make it more sustainable.
Conclusion
By applying the Eco-Value Analysis model and prescribing to DfE guidelines, using the Flex Autoinjector platform as an example, Flex engineers demonstrate the deep understanding and ability to enable an eco-smart circular production model that ultimately reduces waste and generates higher values from resources.
These processes are vital as more industries, especially healthcare, continue to move towards sustainable devices that contribute to environmentally focused goals and enhanced corporate social responsibilities without compromising device reliability and patient safety.
Let’s work together to create the extraordinary
Working with a trusted manufacturing and supply chain partner like Flex allows you to move faster — through ideation, prototyping, engineering, manufacturing, value-added fulfillment, and circular economy solutions and reverse logistics — while leveraging a broader set of expertise, capabilities, and scale.
Flex partners with medical companies to design, manufacture, and deliver their breakthrough medical devices, medical equipment, and drug delivery solutions.
We bring rich technology focus to our design and manufacturing approach with cross-industry leverage at unmatched scale and can provide complete vertical integration under one roof. Our approach is supported by FDA-registered, ISO 13485 compliant, and Med-accred certified facilities and a quality system that holds us to the highest standard.