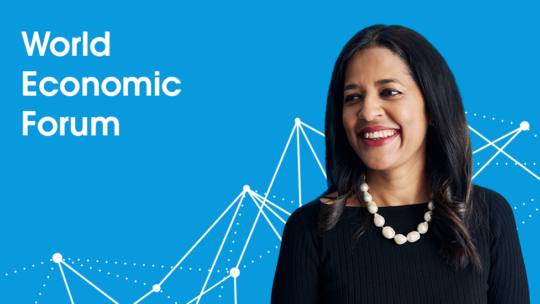
As advanced manufacturing technologies continue to drive efficiencies across the shop floor, Flex’s Paul Baldassari explores how virtual and augmented reality help improve efficiency, knowledge transfer, and more.
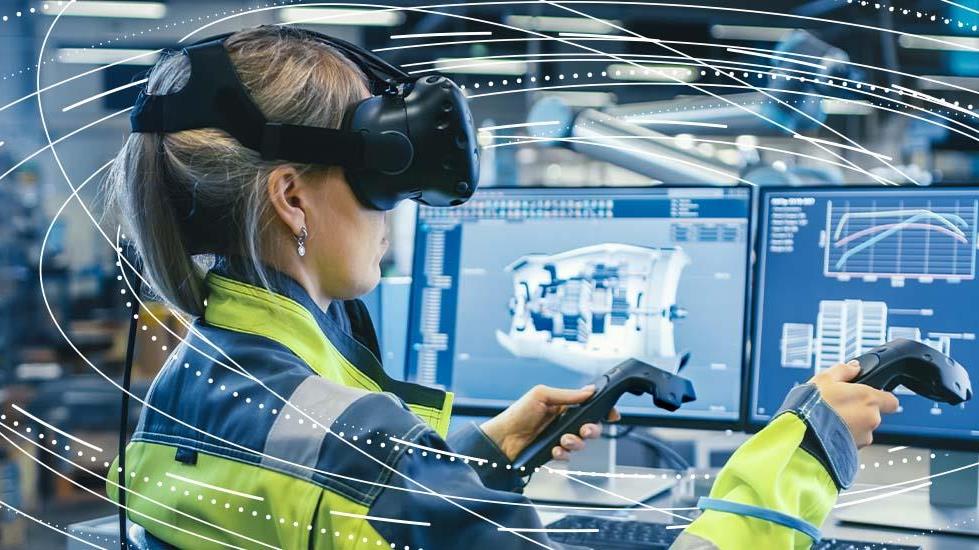
How do Virtual Reality (VR) and Augmented Reality (AR) help drive the next era of manufacturing?
There are many benefits of using AR and VR, especially for manufacturing engineering. One of the main benefits is the decentralization of knowledge and expertise.
Traditionally, most organizations have centers of excellence containing incredibly knowledgeable workers focused on one particular subject. These employees spend years solving challenging problems and gaining valuable “tribal knowledge” based on real-world experience. However, due to geography, organizational structure, and sheer workload, these centers may get siloed and their expertise does not reach other business areas.
AR and VR solve this problem by democratizing expertise and spreading “tribal knowledge” across regions, teams, departments, and functions. The advanced technology moves beyond what can be communicated verbally, written down, or shown in a video. Instead, it provides a virtual, multimodal experience where workers can see, hear, and feel what it’s like to address issues from experts. And since it’s virtual, it helps save time and reduces travel while spreading information. With AR and VR, knowledge is no longer bound by location.
What are some of the challenges of putting VR and AR into action?
AR and VR are dynamic technologies, so organizations adopting these solutions need to be flexible. Often, people forget the amount of effort required to create virtual or augmented reality environments. Even if you have a dedicated team of content creators focused on building these environments, there can still be roadblocks. For example, vendors might not be willing to openly share 3D models of machines, equipment, or other structures. Content creators will need to create these from scratch, which takes time, effort, and resources.
There are also other challenges with hardware limitations, software issues, and end-user adoption. Teams need to consider things like battery life, the field of view, processing power, comfort, occlusion issues, and whether or not end-users feel the solutions can help improve the efficiency of day-to-day activities.
While there can be speed bumps with the AR and VR journey, true ROI comes when organizations recognize the problem these technologies address. These can be pain points such as time savings, multimodal communications, knowledge transfer, or even use cases like remote assistance or work instructions.
What business benefits come from using these advanced manufacturing technologies?
Beyond delivering a revolutionary multimodal experience, there are also some exciting business benefits of AR and VR. But, again, it comes down to pairing the right tools together to solve problems and unlock ROI.
For instance, it’s common to combine simulation with virtual reality. Teams take a simulated view of a factory floor, port it into VR goggles, and customers receive an immersive experience of how a new setup looks. Organizations can use this experience to identify areas they want to discuss that they might not catch on a two-dimensional flat screen. For example, is the line layout conducive to the product design? Did the team miss steps in the building process?
By utilizing these advanced manufacturing technologies together, teams have a much more collaborative design experience that can save time and money by catching potential delays upfront. These tools open substantial business benefits in design, manufacturing setup, quoting, visualization, and more.
Can you cite some additional anecdotes of where and how Flex has used these technologies?
Early in the pandemic, our teams prepared to produce ventilators for the first time in Flex’s history. To accelerate the learning curve and shorten the time to production, we used videos and virtual reality environments to facilitate the training and production transfer processes. We also set up virtual tours to review the production lines on the customers’ factory floors. In addition, onsite production teams wore cameras on their headsets that recorded the processes while providing the narration. One customer even delivered immersive experiences of the existing assembly line using an augmented reality system to capture each required step.
These virtual tools opened new engineering, quality control, and collaboration possibilities, providing an environment that feels like teams are in the same place despite being hundreds of miles apart.
What does the future hold for AR & VR?
The potential and future of AR and VR is that they will be much more immersive and spatial. It will tie into different technologies, such as simulation, digital twins, supply chain, and even shop floor systems. I also think that AR and VR won’t only be on a screen in front of your eyes. It will likely evolve in the form of holograms, projectors, or countless other integrated technologies.
But this is a very crucial time for AR and VR technology. The past 18 months have proved how critical these solutions can be when teams need to be geographically dispersed. However, AR and VR need to continue to prove themselves. It’s been around for a long time and has been on and off the hype cycle. I think the next few years will be critical for the future of AR and VR.