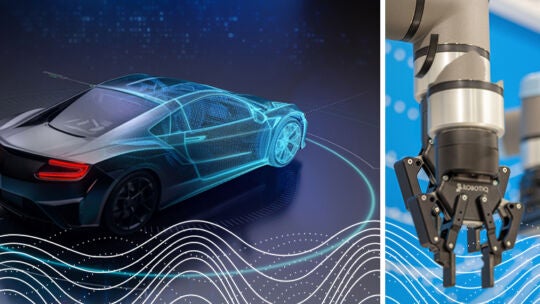
This is the third installment of our blog series, The Supply Chain Resilience Imperative. In this post, we explore how digital transformation can be a powerful lever in building resilient supply networks.
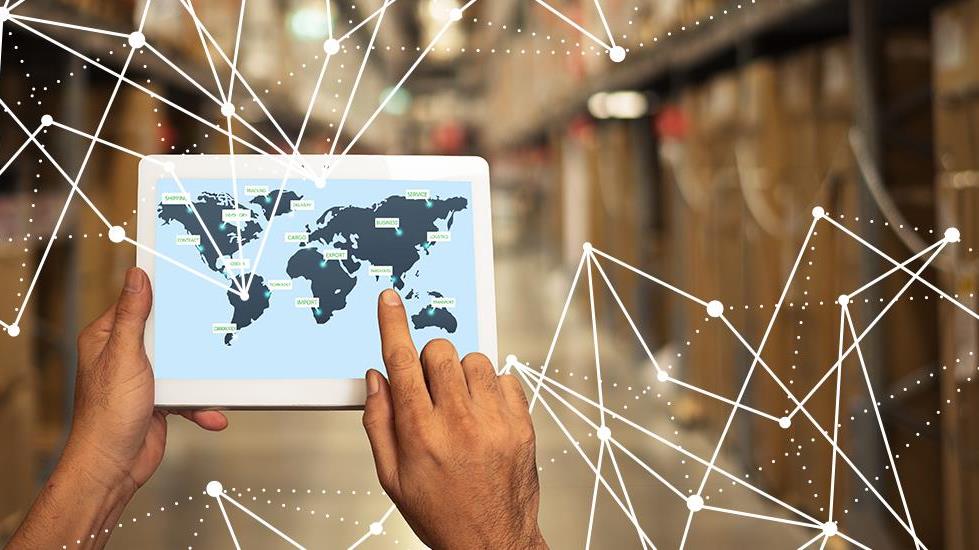
Is 2020 the breakout year for supply chain digitization?
Sure looks that way, if you believe the results of a recent survey finding that COVID-19 has spurred businesses to accelerate the digital transformation of their supply chains by an order of three to four years. If true, this would represent significant progress, as people have talked about supply chain digitization for many years but investment and execution have lagged. Now, with unprecedented access to digitization tools combined with the post-COVID drive for operational resilience, the big leap in supply chain digitization may be on the horizon.
Flex’s digital chain at-a-glance
If you’re ready to take yet another big step forward, how do you select the right approach and tools to maximize your digitization investment? For inspiration, I’ll pull back the curtain to show how we’ve done it.
At Flex, our ecosystem is built on both homegrown and third-party tools designed to help us manage all the key nodes in our supply network. Some of these tools are highlighted here:
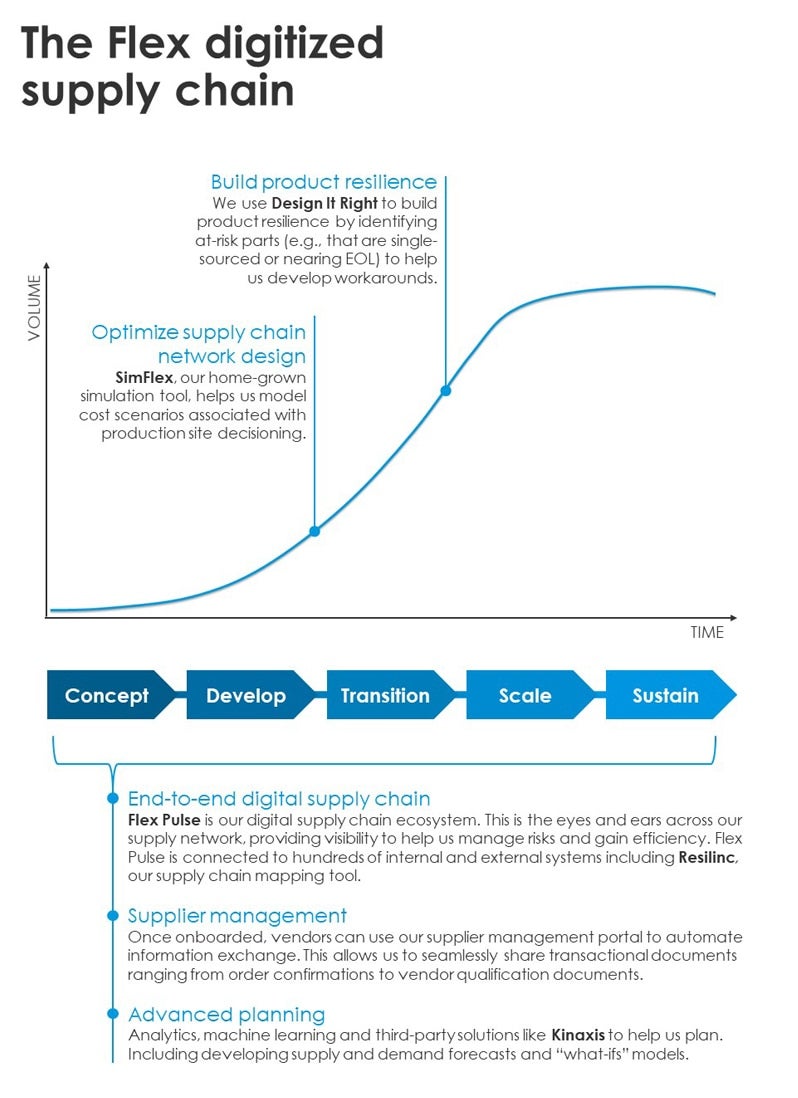
Optimize supply chain network design
When customers engage us to plan for a new product line or enter new markets, the decision concerning where to manufacture and how to distribute weighs heavily.
In these cases, we leverage SimFlex, our proprietary supply chain network design and scenario planning solution. This decisioning tool for locating manufacturing sites and product distribution uses advanced modeling capabilities to simulate and compare scenarios based on key supply chain metrics including landed cost, service commitments and inventory days of supply.
These metrics are computed using wide-ranging inputs such as current and projected inflation rates, crude oil prices, labor costs and other macroeconomic indicators. SimFlex’s data-driven analysis and recommendations boost our customers’ confidence in their decisions.
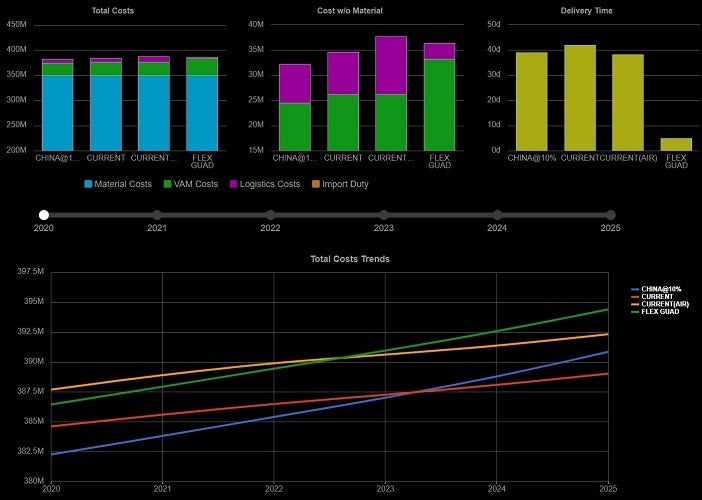
A sample screen from the SimFlex tool which allows for interactive scenario planning and decision-making on manufacturing locations.
Build product resilience
We use Design It Right to help us develop our procurement plan in support of a new product launch. This tool helps to build product resilience by identifying at-risk parts and proposing form-fit-function alternates. To stay agile, we use various sourcing and engineering technologies to help find alternate parts when faced with identified supply constraints.
Communicate seamlessly with suppliers
Our supplier relationship management (SRM) tools, built on Ivalua, are being rolled out across Flex. Using electronic data interchange (EDI) capabilities that automate information exchange between two or more computers, Flex and our suppliers seamlessly share transactional documents such as RFQs, purchase orders, and invoices without any human interference. Once documents land at their destinations, automated notifications and workflows are triggered.
Both Flex and our suppliers can share in the benefits of this system, including reduced costs, faster processing and lower error rates, all making for improved relationships.
Be aware, smart, and actionable
Flex’s Milpitas site awes with its walls on walls of real-time data visualization dashboards representing its supply chain ecosystem. Its no wonder that Flex Pulse is the most widely used tool within our 10,000-strong global supply chain team.
As the eyes and ears of our distributed manufacturing and distribution ecosystem, Flex Pulse is aligned to more than 120 internal processes and connected to hundreds of internal and third-party systems and data sources. Programs and algorithms process this data to produce more than 100 real-time dashboards that ladder up to an integrated view of our entire value chain.
Thanks to these intuitive and real-time visualizations, our teams can spot potential risks ranging from parts shortage to logistical bottlenecks before they become serious problems. We have visibility into the linkages through which our materials move across the world.
In virtualizing our business processes from parts qualification to tracking shipments, we also digitized the physical goods and assets in our manufacturing ecosystem. This means Pulse ingests information down to single parts, allowing us to drill down to a part number by customer with just a few clicks!
When Flex Pulse flags an issue, it triggers corresponding actions for resolution. If there’s a customer change order, for instance, we quickly filter the impacted purchase orders, assign an owner and a tailored workflow will be followed for resolution. Apart from helping us manage risk, Flex Pulse has also helped to optimize our inventory levels, generating cost savings in the millions and improving cash flows.
Since Pulse is part of Flex’s IT ecosystem, teams can access dashboards and resolve issues from their smartphones, laptops and tablets. This is the perfect collaboration tool as the seamless flow of information with flagged issues and actions are visible to everyone across the organization, erasing functional silos and geographic barriers. That everyone from procurement to materials management to logistics sees the same information means we have a single source of truth, allowing us to form a coordinated response and improve collaboration with our suppliers across our production facilities around the world!
Supply chain mapping for risk mitigation
As the world becomes more complex, vigilance is the order of the day. We strive to look deep and wide into our network to mitigate risks by subscribing to multiple third-party data sources.
Beyond trying to get ahead of the next labor shortage or monsoon, we also check our suppliers’ viability on multiple fronts. Today, a key risk area is the Nth supplier. It is not enough to only know your tier-one supplier; we need to better understand our suppliers’ suppliers.
We subscribe to third-party data and news sources to surface risks in our 16,000-member supplier base. We use these services to monitor our suppliers’ financial health as well as their compliance with government regulations and Flex’s sustainability standards.
As an example, Flex Pulse connects to Resilinc, a network mapping solution that provides and analyzes supply network data and presents the information in an actionable manner.
Forecast supply and demand with greater accuracy
As risks rise with uncertainty, supply chain visibility must combine advanced planning capabilities.
Businesses often don’t have the best read on demand, making managing supply chain operations rather challenging. Enter machine learning, which uses AI technology to help improve demand forecasts. Our data scientists build predictive algorithms to help analyze the accuracy of our customers’ demand forecasts and product mix fluctuations using internal and external data sources.
This ability to simulate impact is essential, as it allows us to have constructive discussions with customers and ultimately, develop an optimal response. Additionally, we complement Pulse’s integrated view with Kinaxis’s rapid response demand planning solution. Together, they form the backbone of our advanced planning engine, helping us size up supply changes and quickly plan for constraints and resource allocation.
Outside of rapid response mode, we continuously review sourcing analytics to help us proactively qualify alternative parts to mitigate supply risks. As well, we combine rolling supply and demand forecasts with sales and operations planning to align for the best outcome.
What’s next?
These are exciting times to be reimagining our supply chains. Our industry is well-positioned to take advantage of maturing technologies such as analytics, cloud computing, and data storage to leverage data and improve visibility, collaboration and agility.
A plethora of exciting technologies are before us to take the current transformation to the next level. Case in point is blockchain, a record-keeping technology that can provide transparency and traceability across the supply network. Early use cases include building blockchain-based data management system to reduce fraud by verifying supplier data such as their bank information.
It’s not too early to get your feet wet if you have the budget and staff to experiment and learn about emerging technologies. For instance, Flex is working with several large partners as part of a consortium to explore and collaborate on adopting blockchain for supply chain applications. We are also looking at robotic process automation (RPA) tools to help automate repetitive, manual work, such as routing claims and invoices for processing. We expect these automation tools will help accelerate decision-making and issue resolution.
Supply chain digitization requires substantial investments in time, effort and funding. It’s a long and tough slog, but the rewards of a resilient chain that can stand up to shocks and disruptions are more than worth it.
As you continue to invest in your supply chain digitization, does your team have the skills and experience to leverage the new tools?
Success factors
What are the considerations and success factors in the journey to digitize your supply chain? View the video or PDF to learn more.