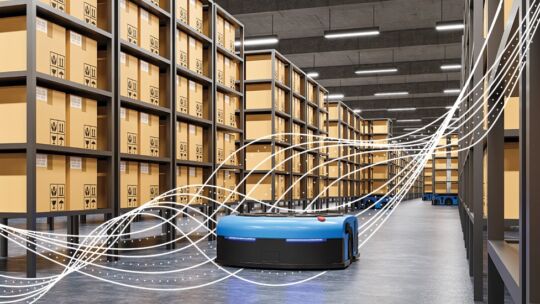
For years, robots have played an increasing role in automobile manufacturing. As the trend accelerates in Manufacturing 4.0, more people worry that a significant number of workers will be replaced by machines that can assemble components with more speed and precision than any person can perform. Implementation of new technology without aggressive training programs, they argue, will result in an employment contraction.
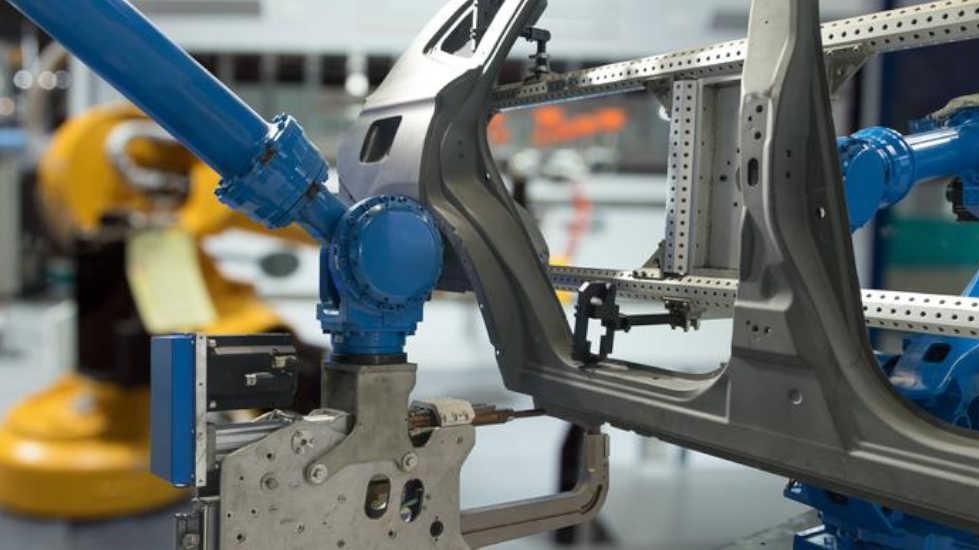
The truth is more nuanced. Automakers began using robots in volume during the late 1980s and early 1990s, notes Tom Mayor, Strategy Leader for Industrial Manufacturing at KPMG. Hauling vehicles around or arc-welding, they were dangerous to be around, but by the early 2000s they’d advanced enough to essentially partner with human workers in tasks like installing dashboards or other integrated components.
Ravin Jesuthasan, a Managing Director with insurer Willis Towers Watson, who has written extensively on how automation impacts the workforce, believes any talk about robots replacing jobs is “patently wrong.”
Automation affects tasks, not jobs.
— Ravin Jesuthasan, Managing Director, Willis Towers Watson
While he expects some routine chores to be taken over by automation, he sees others that will be accomplished by people augmented by robots, and still others that will be completely new. In essence, he and other experts envision manufacturing lines where robots redefine what people learn and do, rather than simply replace them. The automated workplace “will be agile with significant use of sensors and natural language processing to enable seamless interaction between humans, AI, and robots,” he says. “Collaborating with a robot will be similar to how we collaborate with another human — we speak, listen, and see. No clunky interfaces.” As a result, “work will be cognitive and less manual. Think of workers operating digital consoles like a video game.”
If the use of robotics in auto manufacturing isn’t brand new, it’s certainly picking up its pace. “The evolution of tools will be rapid,” says Eric Daimler, Chief Executive of SpinGlass.ai, a development platform for robotics and artificial intelligence (AI) technology and a Presidential Innovation Fellow during the Obama administration. “All levels will need to get comfortable with a constant state of learning new tools. In some sense, we will all be ‘newbies.’ The half-life of new skills will shorten.” Consequently, he believes the ability to quickly acquire new skills will become an important skill in and of itself.
Evolving workers with the process
How, then, do workers prepare themselves to change with their workplace as its technology evolves in unpredictable ways?
“I think the first step here is education and training,” says Schwartz. “This is the responsibility both of our educational system and of employers who require these types of positions.” By investing in their employees, he says, they provide people with opportunities to learn new skills that will make them “invaluable to the growing manufacturing industry.”
Humans and robots are already working together. A lot of assembly line workers already know some basic programming and repair for robots.
— Tom Mayor, Strategy Leader for Industrial Manufacturing, KPMG
Mayor also notes that what’s actually happening to workers may not be accurately reflected in government reports, which often ignore the way jobs are changing. In a 2015 white paper, Darrell M. West, Vice President and Director of the Brookings Institution’s Center for Technology Innovation, made a similar observation. Projections from the U.S. Bureau of Labor Statistics “make few assumptions about emerging technologies,” he wrote, adding that “[it] is hard to be definitive about emerging trends because it is not clear how new technologies will affect various jobs.”
While that may be true, Schwartz believes it’s evident that factories are moving away from being “just rooms with machines and becoming physical/digital ecosystems teeming with software and sensors.” He expects “the role of the factory technician will be redefined, and employees will be better off for it” as they take on work that is more specialized and engaging than “mindless labor positions.”
“The assembly line itself will change dramatically as more of the work becomes cognitive and less manual,” says Jesuthasan. “Think of workers operating digital consoles like a video game. This is going to be infinitely more appealing to younger talent, and also raises the skill premium for the work.”
A pragmatic approach to education
All of this is happening while new, technically adept generations are entering and rising through the workforce. To make sure they have the right skills to satisfy employer needs, Mayor says a number of states and counties are following some best practices.
South Carolina, for one, has a strong network of community colleges, each with an advisory board made up of major local employers, among them auto makers like BMW. When a school teaches computer science or engineering, it focuses classroom work on the field’s core but aligns the curriculum with specific technologies at work in the employers’ facilities. For instance, the lab and project components of a course on programming might emphasize coding applications for robots in vehicle manufacturing.
Mayor notes that advances in robotics and automation are changing not only how products are built, but also how they’re designed. Imagine using 3D printing instead of metal stamping, for example. A vehicle’s components could be designed so they can be created and assembled with robots and people each performing tasks for which they’re best suited. Technology allows manufacturers to develop the optimum mix of people and robots needed to run the production line at peak efficiency.
The entire value chain is going to change dramatically. What is going to be more intriguing is how the product changes.
— Ravin Jesuthasan
As an example, Jesuthasan cites Tesla, which “has changed the way people think about vehicles,” he says. “Instead of buying a product, you now buy a portal though which various services are delivered. Instead of having to buy a new car to get more power, you can now get a software upgrade for your existing car. This is going to create demand for a whole new set of jobs in much the same way the iPhone and the resulting App Store did.”
Mayor believes these changes are happening at an opportune time. At the end of the day, automation is about increasing productivity. With the Baby Boomers exiting the workforce, the smaller following generations will need to be more productive. “We have a lot of people retiring,” he says, “so boy, do we need that productivity.”