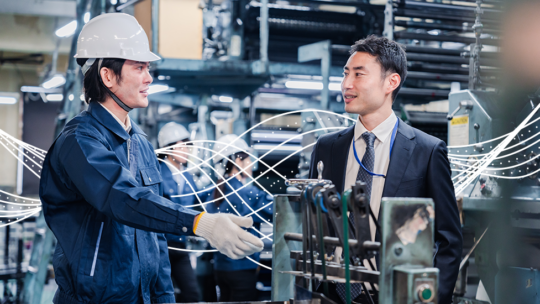
u-blox is a global provider of leading positioning and wireless communication technologies for consumer, automotive, and industrial markets. Within their industrial markets, u-blox also creates medically necessary modules.
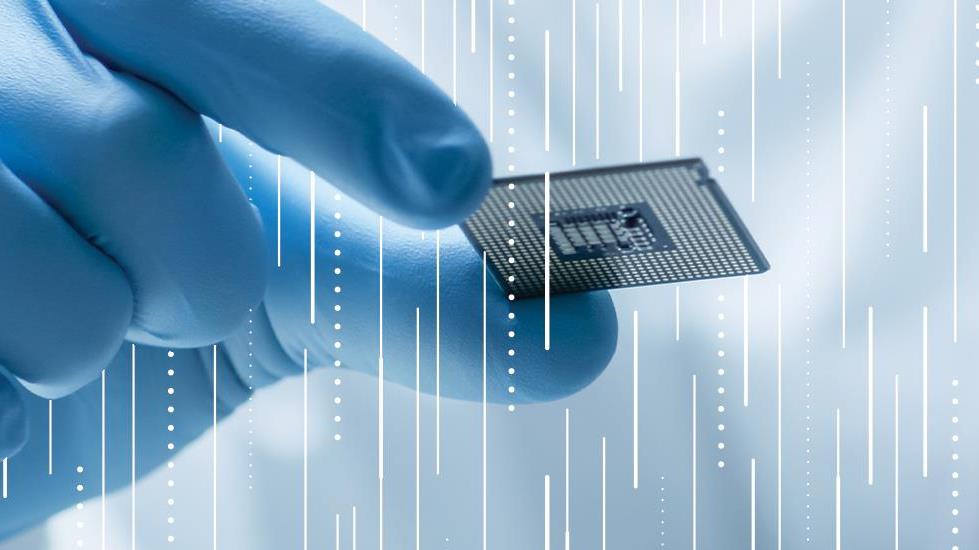
Our supply chain and manufacturing expertise provided invaluable resiliency to the production of their medically necessary modules during the COVID-19 pandemic. You can read about that resiliency in the case study below.
The challenge
u-blox modules require 400 components for manufacturing. Dislocation of a single part halts the entire production line. In early 2020, China issued lockdown orders in response to COVID-19 — and we faced an immediate challenge in securing their required production parts.
We faced further challenges in transporting supplies from China to our production site in Althofen, Austria as other countries mandated lockdowns to curb the pandemic’s spread.
The solution
While we leveraged our supplier relationships to secure production components, the collaboration between u-blox and Flex provided its own deep advantages. With each party having visibility into the other’s key metrics and signals, both sides improved production plans and made better decisions.
Critically, we gained insight into u-blox’s demand base while they monitored our supply chain. This synchronicity was enabled by the data exchange between our respective ERP, MRP and other API facilitated systems.
u-blox monitored everything from stock levels to lead times and modified their planning accordingly. Likewise, with access to data like u-blox inventory levels, we were better prepared to anticipate u-blox demand changes.
This level of transparency not only increased efficiency, it also optimized our service delivery by seamlessly aligning with u-blox’s prioritization of customer needs.
Dramatically reduced transport capacities were another difficulty faced by our logistics team. To answer the challenge, our team worked nonstop with someone on point, immediately untangling any snags to ensure parts could ship.
To ensure success, we proactively rotated team members to monitor supply shipments around the clock and troubleshoot at the first sign of a problem.
With a finger on the pulse of prioritized shipments, the point person maintained communications with both the site team and our logistics provider multiple times a day.
When an urgent situation arose involving a u-blox customer that produced medical equipment, we moved quickly to secure the proper documentation and remove the bottleneck. This fast action allowed the components to priority ship.
In another instance, supply chain disruption threatened critical materials — and only an extraordinary transport time would safeguard production plans. We engaged our logistics provider to execute a hand-carry solution, plotting a course through five hub points from China to Austria.
We monitored the materials during their journey to ensure critical milestones were met. Our extreme diligence ensured these production parts were received on time.
The results
In the end, our production lines remained open to serve essential needs. We delivered on the essential goods commitment on behalf of u-blox and their modules for medical equipment production. In this endeavor, we were privileged to join all our partners in supporting the global medical response to COVID-19.