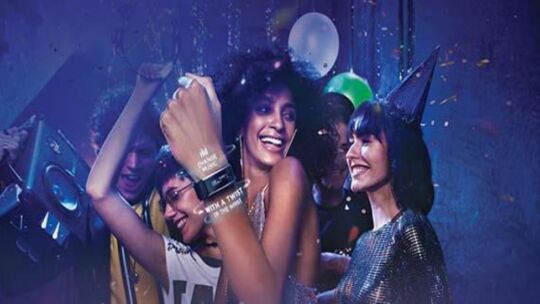
The challenge
A new type of audio speaker based on MEMS technology is set to revolutionize the audio experience for music lovers, gamers, and users of interactive augmented-reality experiences. USound, an Austrian start-up, was founded in 2012. They developed a micro electrical mechanical system (MEMS) prototype for miniaturized speakers which would give users an immersive 3D audio experience. By 2015, they had tested several prototypes in-house and were ready to find a manufacturing partner to scale production.
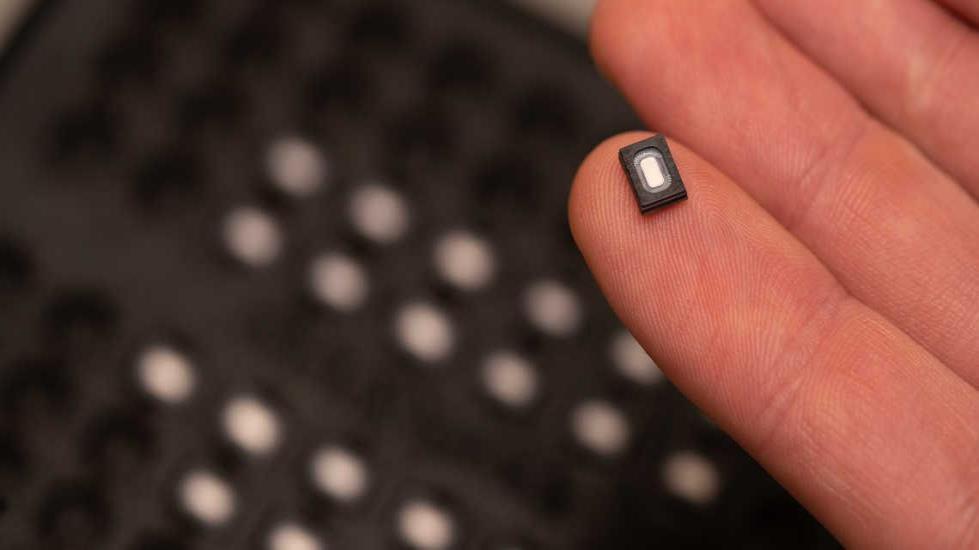
Design for manufacture
Ferruccio Bottoni, Co-founder and Managing Director at USound, describes their position, “As a new kid on the block in audio, we were highly-focused on the design and development of our prototype product with the Fraunhofer Institute in Berlin.”
We were ready to move to the next level and outsource our manufacturing to a third-party, but needed to find a partner with global capability but that also had a local presence.
A mutual supplier suggested we talked to the Flex team at their Product Innovation Centre in Austria, where we would have access to expert knowledge in design for manufacturing and supply chain management.
— Ferruccio Bottoni, Co-founder and Managing Director, USound
Structured methodology
Berthold Jaeger, Director of Business Development at Flex in Althofen, was part of the team which met with USound:
They came to us with a brand-new technology, which was not something we had manufactured before. The prototype design needed careful testing and refinement to ensure the final mass-produced product was stable and of high quality. The systematic approach we take ensures the design is mature enough to be manufactured in high volumes.
The solution
In April 2016, USound was treated to what Berthold calls “the product innovation centre approach.” This gives a new customer access to specialists in technology, design, engineering, and manufacturing in one team, under one roof.
Collaboration for industrialization
The Althofen location allowed both parties to work as a single team which spoke the same language and operated in the same time zone. The geographical proximity of the two companies ensured continuous communication and led to intense collaboration. This allowed materials to be tested, selected, and purchased quickly, while the product design was being refined.
According to Bottoni, collaboration was key to the smooth transition from prototype to launch of the final product. The first phase began with the Flex team analyzing the “lab sample status” product to identify any weakness when it came to industrialization. This also informed the final bill of materials and production process.
Full product lifecycle services
Berthold continues: “Our approach to design and engineering led manufacturing, and knowledge of manufacturing technologies and component materials helped us provide design improvements for USound’s product to ensure it was ready for manufacturing.
Maximizing time
While the analysis and planning phases took a period of months, the investment in a structured approach helped USound avoid rushing to production only to go back to correct mistakes later in the process.
Experience tell’s us that this is where you can waste a lot of time and money.
— Berthold Jaeger, Director of Business Development, Flex
USound and Flex realized that the micro nature of MEMS technology meant the production line for the speakers needed to be fully-automated. The Flex team also recommended building the components in sub-groups to simplify the manufacturing process. “For example, because these units are so small, parts cannot be welded together and must be fastened using glue. The glue is applied in nanolitres — very, very small dots — so specific machines and equipment were purchased to automate the production line,” Berthold explains.
Two-way communication played a huge part in ensuring all parties were aware of progress with daily calls between the teams, monthly face-to-face reviews, and quarterly management updates.
Lessons learned
My advice to any start-up going through the industrialization process is to immediately appoint a dedicated engineering resource to interact with the manufacturing team and, if possible, be on site daily.
Communication is key, and Flex’s open and collaborative approach meant our expectations were managed and issues were addressed in a timely manner.
— Ferruccio Bottoni
The result
The Flex approach to refine and develop a prototype offered USound a template for their own internal structure as they added to their team. For example, as Flex requested an expert’s input from USound on an area like procurement or quality, USound recruited for the role. By mirroring the Flex process and ensuring the required resource was in-house, USound was able to grow its employee and knowledge base.
Volumes grow
Following test runs in November 2018, the first mass produced batch of units rolled off the automated assembly line. Building from an output of 10,000 units a month to 20,000, USound plans to increase production to more than 500,000 units in 2019 and more than one million in 2020. In addition to manufacturing, Flex managed USound’s inbound components supply chain and bill of materials. There are plans to also manage the outbound logistics to original design manufacture (ODM) customers in China and other locations across the world.
Ferruccio says: “Working with a multi-billion-dollar company has meant that the final bill of materials for our miniaturized speakers was very different to the one we had when we first met Flex in 2015! Having access to a global component market place, manufacturing facilities, and an onward shipping network means we can realize our ambitions to be an Austrian fabless company with an international reach.”
Some light on sound
USound’s MEMS technology is seen as the future of audio and has been compared to the impact of LED bulbs on the lightbulb market. The next-generation design is already in development after receiving an additional equity tranche increasing the last financing round to $30M.
Flex has enabled us to produce high-quality, high-volume products and distribute them to our end customers, allowing us to concentrate on research and development as well as sales and marketing.
We plan to continue working with Flex into the future, not only on our current product range, but on new innovations in 3D audio technology.
— Ferruccio Bottoni