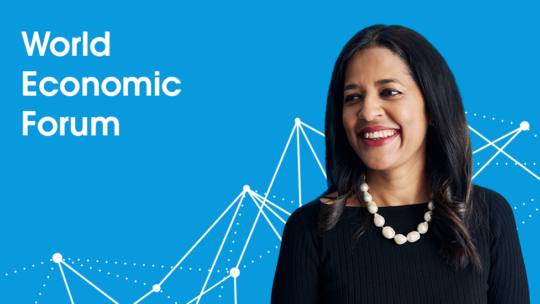
Resiliency is a game of multi-level chess
In early days of the COVID-19 pandemic, travel bans, physical lockdowns, heightened consumer demand and supply chain disruptions challenged manufacturers in every industry. These unprecedented circumstances forced businesses to innovate in the moment, while rethinking almost every aspect of their operations to be more resilient at every phase of the product lifecycle: from ideation to production and beyond.
In this series, Flex manufacturing and supply chain experts will share solutions and unique insights into common hurdles — or “sticking points” — that can slow down or halt businesses.
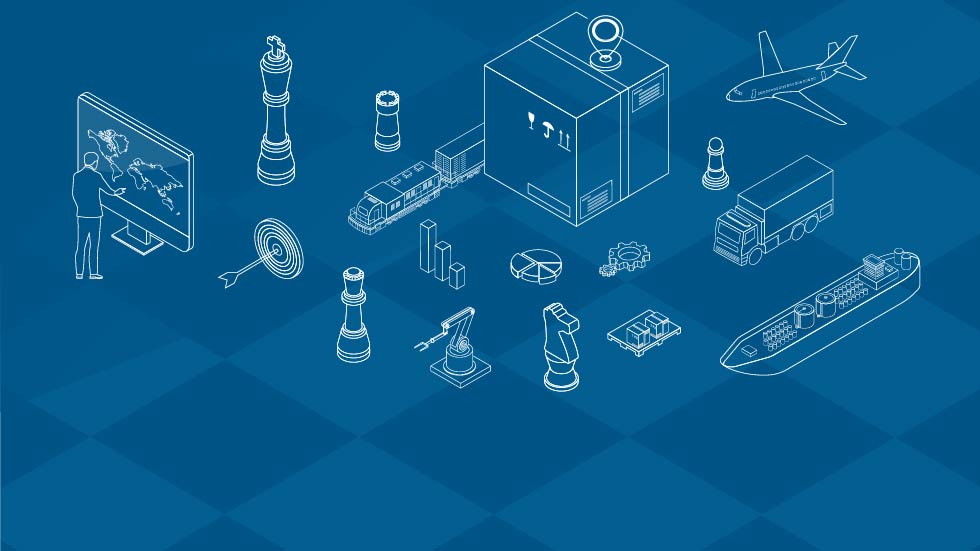
Supply chains are risky business
It’s no secret the past two and a half years significantly altered the way almost every industry across the world operated. With each passing month, new disruptions and risks were introduced, forcing enterprises, business owners, employees and others to quickly adapt and respond.
For supply chains, the pandemic was simply the tip of the iceberg: pandemic and non-pandemic induced challenges and disruptions persisted in the coming weeks and months. Component shortages, the now infamous Evergreen ship blocking the Suez Canal, extreme weather events, natural disasters, trade and tariff wars — even today, the list continues to grow. Supply chain professionals are more aware than ever before that mitigating risk is a top priority.
As supply chain professionals, we’ve faced our fair share of challenges. However, none of these created as lasting an impact on the industry as the pandemic. The COVID-induced supply chain disruptions forced us all to become better and faster at detecting and resolving risk. The most important lesson learned, however, was that the key to success depends on supply chain resiliency. The hard truth is that supply chains are — and always will be — risky business.
While we can’t predict the future, we can better prepare ourselves for how we react to risk, change, and disruption. When it comes to building resilient supply chains, the first order of business is accepting that risk and disruptions do not take place in silos. They’re all deeply interconnected, which means each decision to de-risk has its own impact across the entire chain. Simply put — every decision and every move counts. Let’s look at some of the common obstacles and hurdles that arise in de-risking the supply chain, from design to logistics.
Playing a game of multi-level chess
Like a game of chess, each potential move comes with a unique set of risks, not to mention taking into consideration who your opponent is and the risky moves they might make against you. The difference is that supply chain isn’t just a single game; it’s multi-layered. Picture Beth Harmon from Netflix’s The Queen’s Gambit playing speed chess against 10+ opponents at the same time and you’ll begin to understand what supply chain professionals face daily.
The challenges listed earlier are considered external risks and disruptions that impacted the supply chain. We do our best to predict these, but oftentimes, unforeseen disruptions arise, and we must do our best to respond and pivot in the moment. However, there are several hurdles throughout the product development cycle where we can predict risks and make informed, practical, and strategic decisions to create better outcomes for ourselves and our customers.
Design — Sole source vs. multisource
Anytime you have a sole-source device that comes from a single manufacturing location, you’re going to create more risk. When evaluating the design phase, consider opting for multisource design by identifying alternative sources that can deliver the same technology solution from different geographical locations.
In fact, a recent supply chain survey conducted by McKinsey & Company found that 81% of respondents have implemented dual-sourcing strategies during the past year, an increase from 55% in 2020. Further, 69% said they believe dual- (also known as multi-) source will continue to be relevant for years to come.
If multisource design isn’t possible, known risk must be built into the supply chain solution, such as leveraging different inventory strategies. These options often come at a cost and include risk of excess or obsolescence. They’re not easy decisions, but they need to be made early in the design phase for optimal risk reduction.
Manufacturing — Balancing in-house and outsourced risks and benefits
A key decision when manufacturing is whether to produce in-house, outsource, or leverage a combination of both. Then you can evaluate how to de-risk for the chosen approach, which in turn allows you to find ways to scale with your partner.
For example, when looking at geographical locations, a single manufacturing location may offer the advantage of scale and scope. Yet, multiple manufacturing strategies across several regions closer to end markets can help you achieve greater resiliency and mitigate risk. According to that same McKinsey & Company survey, data showed that 44% of supply chain professionals are developing regionalized supply networks, a notable increase from just 25% in the previous year, and 51% see it continuing to gain traction in 2022 and beyond.
Logistics — Determining efficiency with location
Freight and logistics depend on location, which forces supply chains to make decisions on whether they’ll depend on multiple in-region fulfillment or take a more distributed approach across regions. While a distributed approach incurs more costs, it also carries less risk and offers a more robust fulfillment strategy.
As mentioned in the chess comparison, each of these hurdles impacts the others. Each carries different levels of risks and costs associated with the removal of said risks. A resilient strategy cannot tackle just one piece of the puzzle. The McKinsey & Company research found that 97% of respondents are applying a combination of inventory increases, dual sourcing, and regionalization to boost resilience.
At Flex, we help customers make these difficult decisions with SimFlex, which maps out all aspects of their manufacturing strategies to provide detailed reports on what those decisions will cost in one region versus another. We can forecast scenarios based on current and future projections of inflation rates, crude oil prices, labor costs and other macroeconomic indicators. The analysis and recommendations we provide enable our customers to make informed decisions for their own unique profile and distribution channels.
Resiliency is a journey, not a destination
At the beginning of the pandemic, we often referred to visibility, flexibility, and collaboration as being key building blocks to a successful supply chain. While this remains true, we must also consider that over the last two years, supply chains have faced a level of disruption — both in volume and impact — that is typically seen in a 10-year period. It’s clear that the evolving supply chain risks and hurdles won’t be subsiding.
With this knowledge in hand, it’s important that businesses and supply chain professionals alike remain adaptable as they continue to innovate, deepen relationships with suppliers, and increase visibility into demand. In The Queen’s Gambit, Beth Harmon’s skill and strength as a player did not preclude the fact that there is always another opponent to face. Similarly, no matter how strong your supply chain is, you must be ready to confront the next disruption. Although we’ll never fully remove risk from our supply chains, we can make smart, informed and strategic decisions that enable us to counter move risk with resiliency. Check mate.