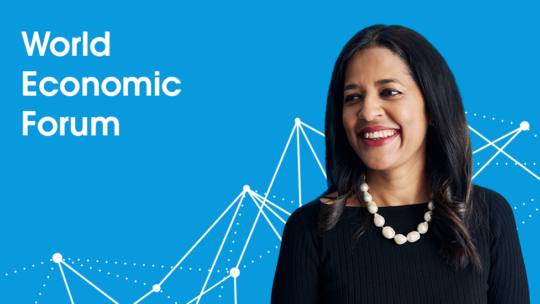
A previous post in this supply chain resilience blog series made the case that profound global risks — currently exemplified by the COVID-19 pandemic — have put us at an inflection point. This moment has become a rallying point to fortify our end-to-end manufacturing ecosystems as COVID-19 has laid bare their vulnerabilities. In this installment, we explore the various levers of resilience and use Flex’s own experiences as a case study for applying them.
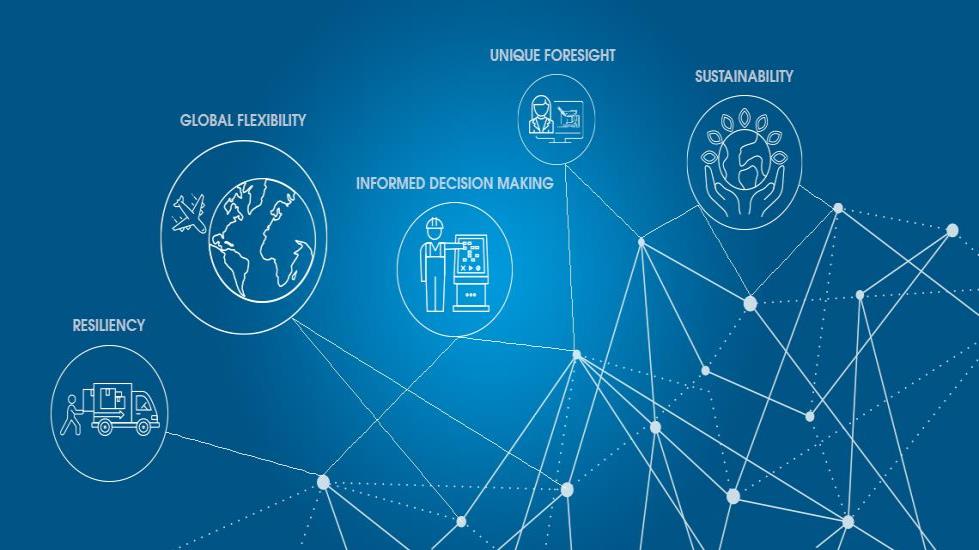
What resilience looks like
If your supply chain is resilient, your production and distribution systems can continue to function as well as is possible in a destabilizing event. Indeed, a key indicator of your operations’ resilience is the degree to which you can meet your obligations to your customers — despite disruptions — by consistently delivering goods and services against your cost, quality, and ESG standards.
To get there, risk mitigation measures must be embedded with clear accountability throughout the chain from procurement to last-mile delivery. One way to develop these measures is to consider the resilience dimensions that need to be continuously strengthened within your operation — and where along the chain they need greater reinforcement.
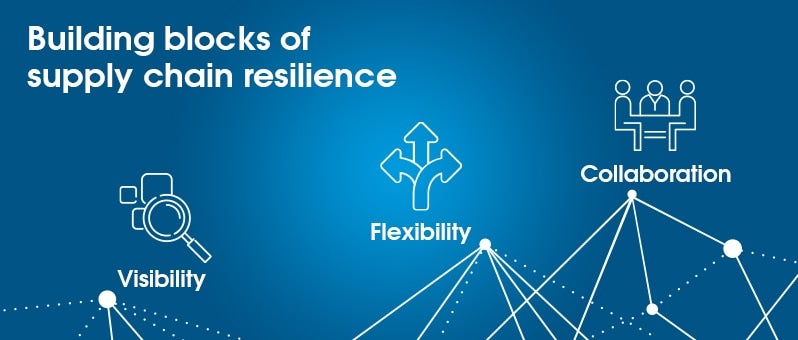
We suggest flexibility, visibility, and collaboration as the key pillars to reinforce your production and distribution systems. Multiple studies have found these to be among the leading attributes of resilient chains. Flexible organizations can adapt to disruptions with minimal impact. For example, one way to build flexibility is to develop multiple suppliers in the event of service interruptions by your primary suppliers.
When it comes to gaining visibility, this is absolutely critical to help you anticipate risks in real time, whether it’s understanding a weather event such as the path of a monsoon or the ESG reputation of a second-tier supplier. Finally, collaboration entails bringing together stakeholders to work towards a common goal, and this includes information-sharing both inside and outside of the organization. The stronger the collaboration between companies in a supply chain, the faster and more effectively they respond to disruptions.
A risk management framework
As an organization managing some 1,000 supply chains on our customers’ behalf, Flex is constantly evaluating our risk mitigation models.
We identify, evaluate, and mitigate risks through three lenses:
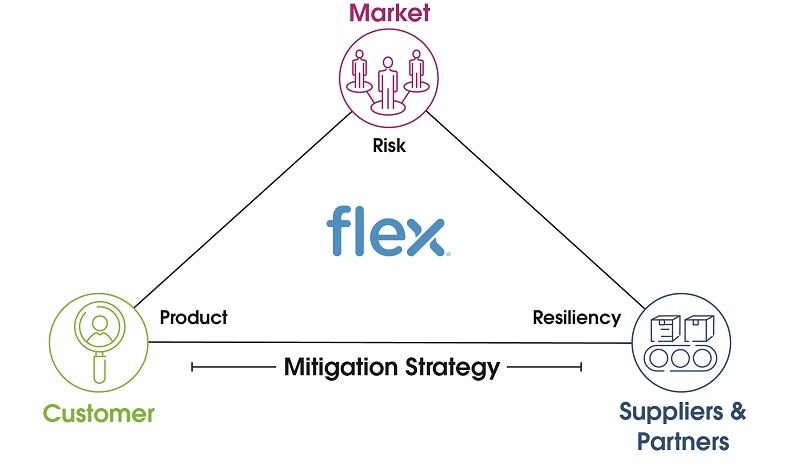
1. Serving our customers
Understanding our obligations to customers requires an understanding of the risks in the chain. This begins with identifying the most critical components and mapping out their associated risks. For example, are there seasonal shortages of critical parts or potential price fluctuations that we need to plan for?
2. Taking the pulse of our suppliers and partners continuously
How financially stable are our partners? Are there emerging risks to quality and timely shipment?
3. Keeping tabs on potential marketplace disruptions
These include political, environmental, and other external threats.
Operationalizing visibility, flexibility, and collaboration
Building a strong supply chain is a proactive de-risking process that never ends. Like any insurance policy, it comes with a cost. With your core goals and resources driving your investment decision, there are multiple tools and tactics at your disposal. This table shows how various risk mitigation strategies could be applied across our three pillars.
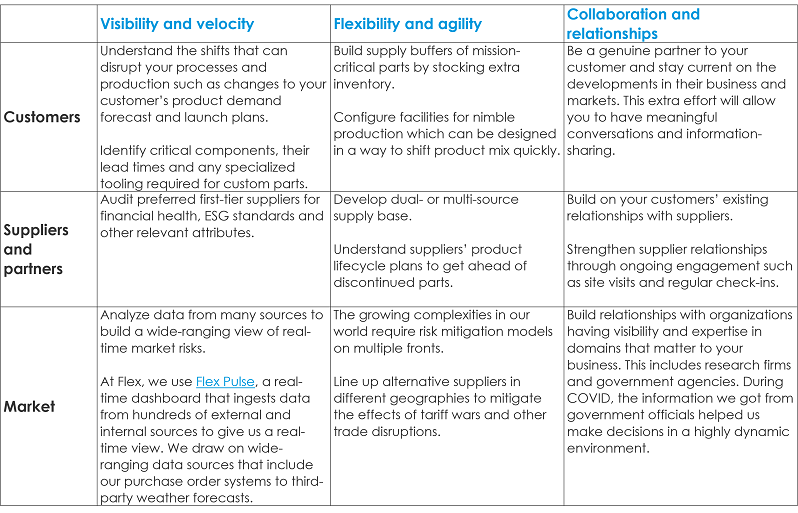
Designate teams and assign accountability
With the risk mitigation plans in place, it is critical to ensure accountability throughout your organization.
At Flex, we have a company-wide global resilience team tasked with diffusing risks in the event of serious threats and large-scale interruptions. This team prioritizes the protection of Flex assets and those of our customers and partners, which include human resources and intellectual property.
When it comes to the particulars of a specific product line, these are managed by a strategic supply chain team that oversees all related operations. As the first line of defense when issues arise, this team constantly assesses risks and collaborates closely with planning, procurement, and other teams to optimize operational shifts and decisions specific to addressing the product and customer needs.
Specifically, the strategic supply chain team analyzes the risk profiles of the key inputs along the product’s lifecycle from beginning to end.
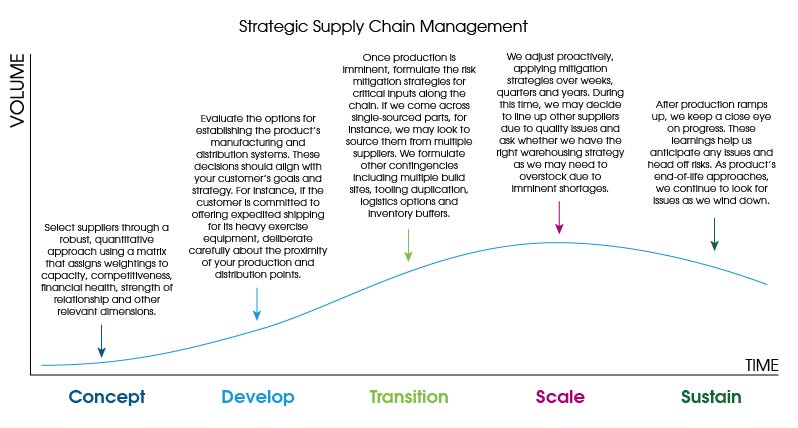
Resilience in action
How do all of our advance preparations play out in real life?
During the COVID-19 crisis, we received early warnings from our team in China. Utilizing dashboards in our Flex Pulse system we wasted no time in taking action. Our global resilience team immediately engaged as the ground-zero command and control center. By instinct, collaboration became the order of the day. Our China teams guided us through pandemic risk reduction best practices, including how often to change masks and how to sanitize and deep clean our factories.
In parallel, we set up war rooms around the world hosting executive meetings every day. This cascaded into many follow-up conversations and action items with cross-functional teams worldwide to identify solutions around the clock.
Tiger teams on the prowl
The supply chain organization held global daily calls along with the resilience team and other cross-functional peers. Our first priority was to understand all the parts originating from China, and freeze the current order status, ensuring no open orders were pushed or cancelled. To gain visibility into the actual supply and demand, we then reconfirmed forecasts with customers and orders with suppliers to verify that what was on order was still required by customers and produced by suppliers. Everyone pitched in and the information became visible and actionable via Flex Pulse real-time dashboards.
Once we sized up supply and demand the best we could, we needed to figure out how to move the parts to meet production schedules then deliver the finished goods. Through this highly fluid situation where we were operating on imperfect information, we wanted to hear everyone’s voice. We had many daily discuss-debate-decide moments in rapid succession as the number of decisions required each day stretched over 12 to 16 hours at the height of the pandemic.
Overcoming challenges through agility and strong relationships
During this time, shortages became an issue, and this hit our healthcare solutions group particularly hard. The team went from experiencing normal shortages for around 25 parts in late January to shortages of hundreds of parts within weeks. Some relief came by way of the strong collaborative relationships we have established with our suppliers over many years, which enabled us to dramatically reduce the replenishment cycle for certain key parts while securing commitments for continuous shipment.
For other critical parts in short supply, we had standing workarounds. For instance, we had engaged our engineers to identify and test viable substitution parts during the pre-production design and tooling phase. Taking this extra step meant we were ready to source the substitute parts — and this proved to be a worthwhile investment during the COVID-induced shortages.
Our decision-making capability was enhanced by information our teams were able to glean from our network of relationships which also includes government bodies who gave us insights into the pandemic’s trajectory and potential border closures.
Bringing together internal and external stakeholders and their multi-domain expertise put us on an agile and decisive path to problem-solve at scale.
Looking back and looking forward
Resilience is not about investing in a single tactic or technique; instead, it is a proactive process that continuously incorporates new learnings. In this vein, consider building a roadmap for making your COVID-19 lessons actionable. What insights have you gained into your chain’s weakest links that you can leverage to help you be better prepared for the next disruption? What are the critical investments to make in light of these weak links?
At Flex, we saw the payoffs from our investments in building strong foundations and contingencies that helped us adapt to the challenges resulting from the pandemic. Is our supply chain bullet proof? Certainly not. Supply chains will never be completely risk-free — the key is to install the right talent, infrastructure, tools, and culture to achieve business continuity and to continuously identify opportunities to fine-tune your risk management practices.
As there are many tools in the resilience-building toolkit, in our next post, we will dive into the technology tools that have great potential for developing flexibility, visibility, and collaboration to help you beef up your chain.