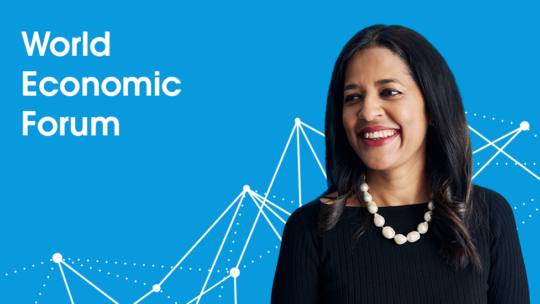
Supply chains are being thrust onto center stage as never before. As a confluence of events has brought supply chains to various moments of reckoning over recent times, we dissect the ins and outs of rebalancing the manufacturing ecosystem in this blog series. In our first installment, we review the global landscape to size up the impetus for systemic change by restructuring our end-to-end production and distribution processes.
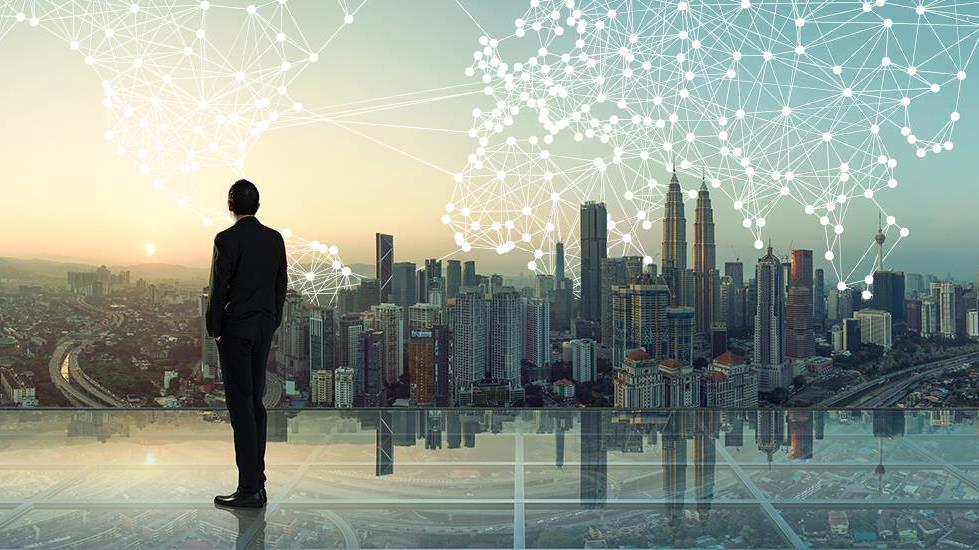
Amnesia and misaligned incentives may be among our worst enemies when it comes to building supply chain resilience for the long haul.
History says we tend to return to business as usual in due course in the aftermath of a crisis. Naturally, this includes returning to the bias towards under-diversified supply chains which has been identified in more than one study. Following major disruptions, finding a solution to address them becomes top priority, and investments are made to fortify the supply chain, including diversifying the supplier base.
Flex supply chain fast facts
1k
supply chains
1M
component SKUs
16k
suppliers
$500M
freight spend
25k
purchase orders executed daily
30
countries we operate in
$30B
direct material spend
10k
supply chain professionals
Over time, however, these costs become burdensome. As the returns on preparing for rare catastrophic events are seldomly immediate, managers often revert to their pre-crisis mode in a bid to gain cost savings. After all, financial targets and other corporate practices reward efficiency and low cost.
As explained in one of the studies, we don’t have enough experience planning for black swan events for the simple reason that they are rare. Because we lack an understanding of such shock events, we also tend to underestimate their impact and forget the lessons learned once they become a distant memory.
Will be it different this time?
With COVID-19, however, we may have reached a tipping point to reengineer our end-to-end chains at scale. The contagion was an unprecedented globally destablizing event with its initial epicenter being China, the well-calibrated site of the world’s manufacturing ecosystem. Today, the havoc wreaked by the pandemic is as fresh as ever. With reduced consumer demand for air travel, for instance, many are feeling the pinch of reduced cargo capacity as 40 percent of all shipments were handled by commercial aircraft pre-COVID.
Even before the pandemic, powerful environmental, technological and political forces were already feeding an appetite to redesign corporate strategies and operations. The geopolitical undercurrents against open trade that preceded COVID-19 were motivating businesses to find ways to manage tariffs and other government-imposed cost regimes. Add to this the alarm bells that scientists and researchers have been sounding about various global risks which may finally be heeded in the wake of COVID-19 — and you have the ripest conditions yet to overcome entrenched human behavior and force a restructuring of corporate value chains at scale.
Cost takes a back seat to security
The repeating cycles of forming a crisis response only to revert to the status quo may finally be broken in a world fraught with rising risks.
Indeed, in the post-globalization era, it’s no longer only about driving down costs and increasing efficiencies but ensuring reliability across the value chain. As the world’s complexities and uncertainties continue to grow, so do risk exposures.
On the climate change front, scientists have warned of more frequent and extreme weather events. Weather problems can severely compromise upstream and downstream inputs, from labor to critical infrastructures like roads and transport. Accordingly, business leaders are recognizing climate change fallouts. Climate issues now rank as the top five risks by probability for the first time since the World Economic Forum (WEF) began surveying stakeholders for its annual Global Risk Report. Similarly, WEF’s 2020 Regional Risks for Doing Business Interactive Map shows environmental risks getting increased attention from executives. Notably, water scarcity also rose to prominence in the latest WEF global risk report, even though most businesses are still shrugging off this risk owing partly to the cheap cost of water.
In the virtual realm, large-scale cyber-attacks can also cripple supply chains, and such attacks against businesses have become more damaging and frequent.
As the pandemic has demonstrated, a crisis can wreak havoc on a global scale and over-reliance on a consolidated supply source can come at a high cost in times of disruption. With multiple uncertainties on the horizon, putting security measures in place against disruption may increasingly trump their implementation costs.
The hand of government
As supply chains have become a matter of national security in the aftermath of COVID-19, governments are addressing systemic risks in our chains and calling on businesses to cooperate.
Last month, the European Union joined the chorus call for regionalization, amplifying the need for “strategic autonomy” and “secure raw materials supply” in a series of European Commission summits and communiques. These talking points are part of Europe’s broader plan to develop resilient supply chains, strengthening raw materials sourcing within the region, and reducing dependencies on third countries. Also last month, President Trump issued an executive order for the United States to develop a secure precious minerals production capabilities in partnership with industry. Meanwhile, Japan earlier this year earmarked funds to incentivize businesses to diversify their supply base throughout the world and repatriate their production ecosystems.
The government’s incentives and mandates — and disincentives like tariffs — have the potential to drive large-scale supply chain reorganization. Following a skirmish with China in 2010, for instance, Japan sought to reduce its Chinese rare earth materials imports which made up 58 percent of its total supply in 2019, down from 82 percent in 2010.
The upshot? Government can play well with the private sector through rational mandates and the right incentives.
Offsetting risks and trade barriers
If the pandemic has taught supply chain managers anything, it is that over-dependence on any one partner, country or region can lead to critical issues and challenges. A diversified supplier base will usually cost more than a consolidated one; likewise, migrating a supply chain to regional markets also requires a hefty upfront investment. Yet the tradeoffs between security and costs must be weighed and failure to adapt in today’s highly dynamic world could lead to poor outcomes with dire financial consequences.
Given our increasingly complex and interconnected world, sudden shocks are more probable than ever. Every 3.7 years on average, businesses can expect a supply chain disruption that lasts at least a month, and the most serious of these can have severe financial consequences, according to a 2020 McKinsey analysis.
This forecast coupled with present trade barriers and imminent global risks presents an opportunity to take proactive measures. Devising a continuity plan before the next disaster strikes can help minimize supply chain disruption. Managers would also do well to assess their top risks and understand the corresponding risk profiles for each supplier. Businesses can take steps to earnestly plan for black swan events, capitalizing on the fresh lessons learned from COVID-19 to explore alternative ways forward.
The critical precursor to tackling all the challenges facing supply chain managers will involve managing key tradeoffs — including striking a balance between security and costs so that your supply chain can withstand more frequent disruptions.