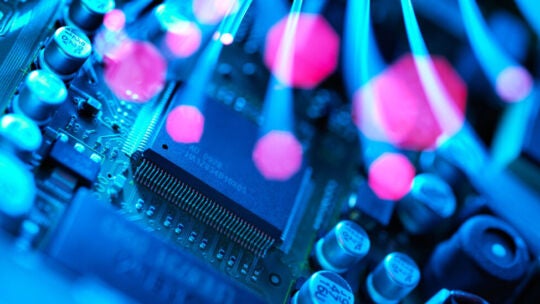
On behalf of a leading cloud infrastructure provider, our team in Penang, Malaysia builds printed circuit board assemblies (PCBA) that enable cloud computing. These assemblies serve as a gateway to the cloud for servers and other computing devices. One in eight online interactions routes through a PCBA we built!
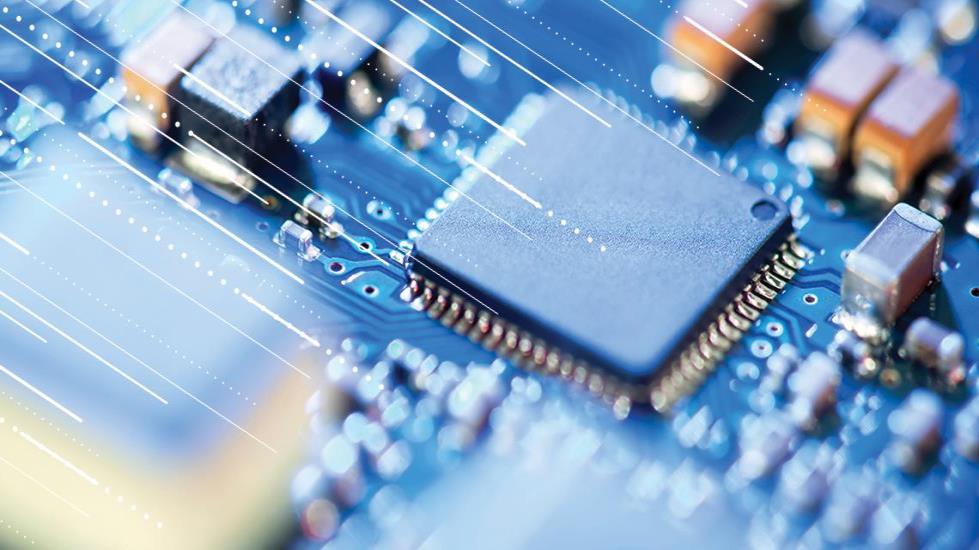
The Challenges
We experienced significant COVID-19 resource and manufacturing challenges over a sustained period.
March–June, 2020
Combined with a previous backlog, our customer saw a demand surge for PCBA products at the outset of COVID-19. Online traffic spiked as people worked, shopped, socialized, and streamed entertainment from their connected devices.
During this period, China went into lockdown and raw materials became scarce. Our Penang production site receives many of the customer’s raw parts from China. We had to carefully manage the material shortages to ensure we could meet demand.
At the same time, the Malaysian government ordered a “partial lockdown” to curb the spread of COVID-19. As a result, all businesses except for those in critical services and industries were required to suspend operations.
July–September, 2020
In July 2020, our customer was in critical need of delivering 50% more PCBA within just four weeks. To meet this target, we needed to scale to unprecedented levels.
The Solution
March–June, 2020
Three days after the mandated lockdown, our Penang team secured government approval to gradually restart production of these goods — they were recognized as essential, and we successfully demonstrated our plan to keep our employees safe. Initially, operations resumed at 15% of capacity; by May, we had permission to increase capacity to 50%. A month later, we were able to return to 100% capacity all while maintaining a safe environment for our employees.
As production resumed, we changed our manufacturing approach. Instead of relying on the existing “one-piece flow” operations, which was optimal pre-COVID-19, we reconfigured our manufacturing process. We dispersed the product families as “islands” which provided the space required to keep our teams safely distanced.
The “island” concept created seamless product flow, generating a 25% efficiency improvement. This improvement coincided with the easing of the raw material shortages and our frontline teams quickly made up lost time and fulfilled the demand surge.
July–September, 2020
To ensure we delivered on the customer’s new volume requirements, our Penang team tapped our staff in Zhuhai, China to qualify a second factory location and augment current production capacities.
The Penang team jumped into action, coaching our Zhuhai peers to a successful on-ramp. This involved a “virtual qualification” where we demonstrated how each quality indicator would be met. Consequently, the customer did not need to conduct an in-person audit, saving valuable time by compressing the factory qualification process.
Although the Zhuhai team had experience in manufacturing the assemblies, our Penang team accelerated their learning curve by providing them:
- Thorough training and tribal knowledge transfers
- Deep support for product qualification
- Constant progress reviews over multiple shifts; this oversight enabled Zhuhai team’s scout build to be near perfect
Success factors:
- The Penang team assisted their Zhuhai colleagues with qualifying tooling and processes rapidly. Penang team members quickly made adaptations to the machine platforms while providing engineering data and documentation in quick succession.
- Our Penang team also localized and adapted the customer’s product profiles to Zhuhai’s manufacturing set up and standards, accelerating the onramp. It was our Penang group’s product knowledge, developed over many years, that enabled the Zhuhai team to ramp up so quickly.
- The knowledge transfers and handoffs were not a case of simply using the Penang team’s parameters. It involved the application of deep knowledge expertise, fast, disciplined execution, and Penang engineers working with the Zhuhai team to develop the right “settings” that worked for a multitude of variables.
The Results
Our Zhuhai location qualified their first PCBA in just four weeks — a record time and an incredible accomplishment.
The teamwork and shared value in “doing whatever it takes” enabled the flawless execution for our customer.
We shipped more than a million assemblies to the customer between June and September, a record quarterly volume in our 20-year partnership — and did so under constrained conditions.
Amid a lockdown and reduced capacity, our Penang team continued to deliver extraordinary service with ingenuity, dedication, and forward thinking.