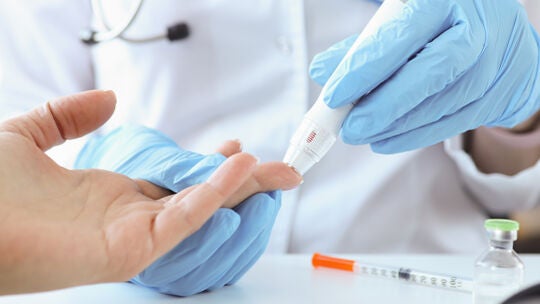
Background
A leading medical equipment company selected Flex to manufacture their Class II diabetes product. In the United States, the Class II medical device designation refers to those devices with a moderate to high risk to the patient and or user. More than 40 percent of medical devices fall under this category. They require the utmost reliability, as any mistakes or issues in the design or manufacturing process could put patients at risk.
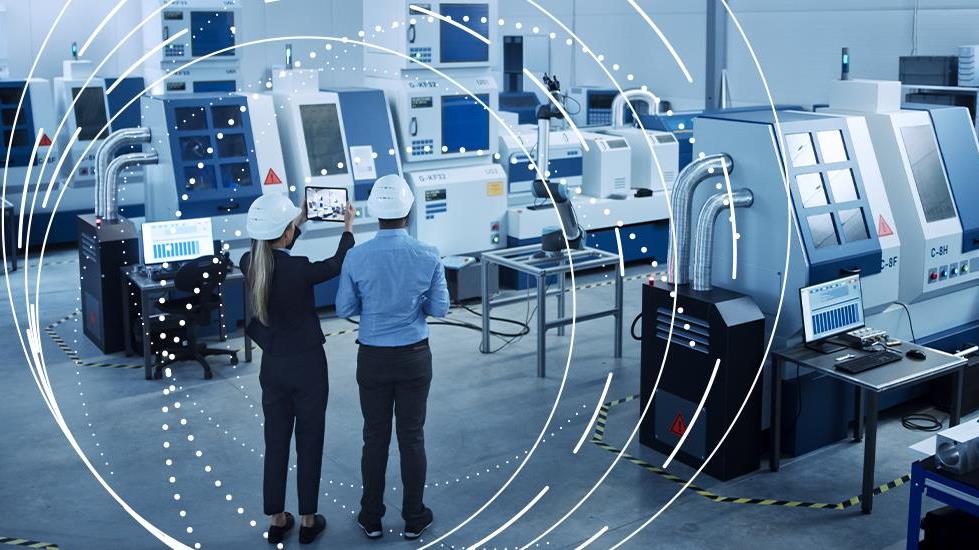
Establishing compliant manufacturing processes for medical devices can take years due to the stringent performance, reliability, and safety specifications involved. Additionally, any modification to those processes requires revalidation, documentation, and resubmission to regulatory committees, a time-consuming and costly process that can cause delays. Balancing all of these considerations and priorities, it can be challenging for medical device manufacturers to streamline processes for greater agility and resiliency while still meeting all regulatory requirements.
Given the high stakes of a patient’s well-being and the need for precise planning and forecasting, medical device manufacturing is an ideal candidate for simulation technologies that use software-based environments to optimize processes. One such technique, discrete event simulation (DES), models the operation of a real-world system as a sequence of discrete events. It allows us to safely and accurately model, simulate, and analyze the necessary relevant assembly, testing, and shipping processes.
DES accelerates time-to-market and reduces costs significantly by enabling us to:
- Design an efficient flow of people and materials
- Predict yields more accurately
- Reduce inventory
- Increase throughput
Challenge
As the healthcare industry adapted to the pressing needs of the COVID-19 pandemic, medical professionals also had to pivot and become more resilient so they could continue addressing other critical healthcare demands. We needed to help our customer accelerate and optimize the development of a Class II diabetes product to ensure speed, quality, and reliability, while scaling up production and minimizing risk through the ongoing challenges of a global pandemic.
Solution: Optimize manufacturing using DES to create a digital twin of the factory floor.
With this virtual representation of our complex production system, we tested various scenarios and gained insights on optimization tactics.
First, we imported representations of the production assets, like equipment, layout, and staff, into the DES software to mimic the physical production process. We also analyzed how equipment in the environment related to other equipment, people, materials, and other objects. This provided a baseline for the process flow.
With the process flow in place, we then loaded relevant data and assigned them to the appropriate asset, creating a digital twin of our factory operations. This enabled us to simulate processes without expending equipment or materials, iterating hundreds of thousands of “what-if” scenarios. When the tests were completed, our business and engineering staff worked with our simulation experts to review the output for further optimization.
We focused on several key dimensions, including:
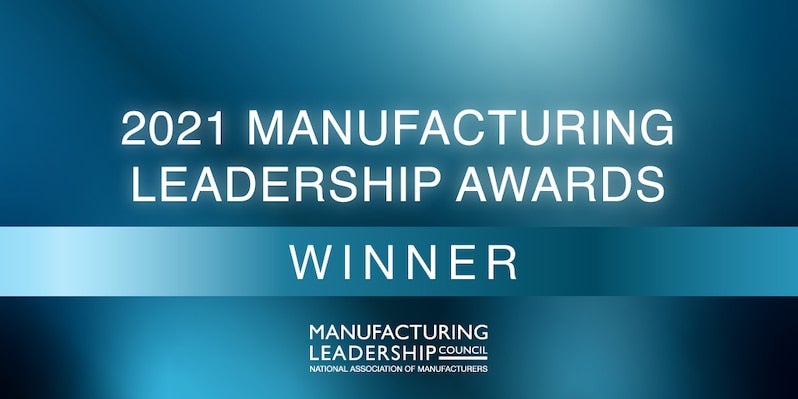
- Improving yields
- Utilizing carts to remove bottlenecks for value-added processes
- Evaluating the master schedule to increase delivery from 5.5 million to 8.1 million units per quarter
- Optimizing work order sizes to deplete material in the given unit
Results
Without simulation, this testing process would have taken at least three months longer. But our DES tool allowed us to complete our optimization analysis in only three weeks, enabling our customer to get the product to market faster. This saved our customer time — and money. It also tested the process to ensure it would yield a reliable product, a critical success factor for Class II medical devices. Using our simulation expertise to optimize production processes, we helped our customer achieve significant ROI.
For example, using more carts to transport material and work-in-progress products around the factory for value-added processes introduced greater process efficiency. Without performing simulation, we would not have identified carts as a solution to unblock potential bottlenecks and achieve greater resiliency.
Major efficiency gains included
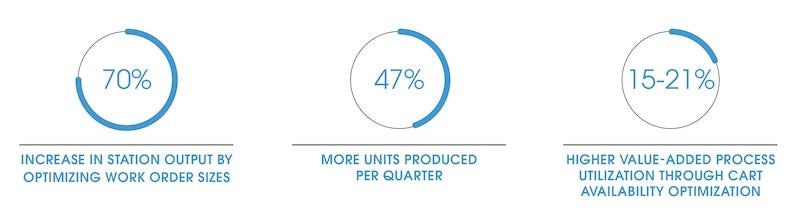